
ESG and ZEECO
OUR COMMITMENT
At Zeeco, we are committed to cultivating a safe, inclusive, and responsible work environment. As part of our commitment, we engineer and produce products, services, and solutions that contribute to a sustainable future. In doing so, we drive long-term business value while acting as a steward of our people, the environment, and the communities we serve.
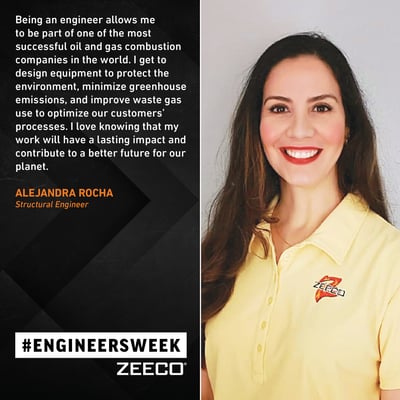
Methane & Carbon Dioxide Emissions Reduction
Lower emissions and operate more efficiently by flaring less, flaring better, and preventing fugitive emissions.
According to the EPA, methane (CH4) and carbon dioxide (CO2) accounted for 90% of all U.S. GHG emissions driven by human activity in 2019. At Zeeco, we look to mitigate the level of GHG emissions from the combustion of fuels, leaks in natural gas systems, and more.
Thought Leadership Forum: Methane & CO2 Emissions Reduction
As new GHG emissions regulations go into effect, Zeeco is committed to providing resources, technology, and support to help companies comply. Play the YouTube video above to hear Zeeco's flare system experts discuss CO2 and methane, identify key areas of focus to reduce emissions of those GHGs in the oil and gas industry, and evaluate tools available today to help meet climate goals.
Reduce CH4 and CO2 Emissions by...
Flaring Less
Flare systems are necessary to keep personnel safe and prevent potentially harmful emissions from venting into the atmosphere. Although, non-safety-related (routine) flaring results in the unnecessary waste of otherwise usable fuels and contributes to millions of tons of CO2 emissions annually.
Achieve Zero Routine Flaring Before 2030
Zeeco offers a number of solutions to support the World Bank's Zero Routine Flaring by 2030 initiative and help eradicate the routine flaring of approximately 140 billion cubic meters of natural gas each year.
Save Fuel and Boost ROI with Flare Gas Recovery
Zeeco designs systems to work with existing flares to help eliminate non-safety-related usage. With the properly engineered and designed system in place, waste gases are recovered, processed, compressed, and returned to the plant to be reused as fuel rather than flared. This process reduces both fuel and flare maintenance costs.
Zeeco’s Flare Gas Recovery (FGR) systems will pay you back through fuel savings and help your plant meet current and future regulations by dramatically reducing CO2 emissions.
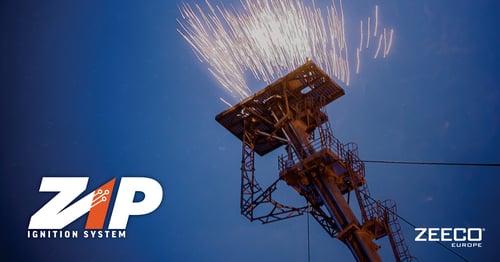
Eliminate Continuous Pilot Fuel Gas Usage with ZIP™ Ballistic Ignition System
In situations where flaring cannot be avoided, such as emergency reliefs, steps can be taken to reduce associated emissions. For example, flare systems require an ignition source to ignite relief gases. While direct electrical spark technologies, such as flare pilots, are often required to ignite relief gases, they require a continuous supply of fuel gas to feed a flame at the flare tip exit.
The ZEECO® Zirconium Instant Pressurized (ZIP) ballistic ignition system achieves more reliable ignition than direct electrical spark technologies and does not require a continuous supply of fuel gas. Instead, the system utilizes zirconium-filled pellets and a striker plate to shower the flare tip exit with sparks and ignite the flare gas.
When used in tandem with a flare gas recovery unit and a liquid seal, zero hydrocarbon emissions can be achieved during continuous operation.
Flaring Better
The use of more efficient flare systems in the field is critical to lessening the environmental impact of day-to-day operations. Zeeco offers combustion electronics to take the guesswork out of the combustion process and provides engineered solutions to achieve safe and smokeless flaring - anywhere in the world.
Take the Guesswork Out of the Combustion Process
The FlareGuardian™ direct flare monitoring system measures combustion efficiency (CE) in real time, allowing operators to achieve - and verify - true CE (often 99.5% or higher) well above typically assumed rates (98%). Zeeco’s Contour™ delivers automated, real-time, direct monitoring, as well as smokeless injection media control at a fraction of the cost of indirect measurement systems.
Mitigating Emissions to the Air
To prevent emissions to the air, it is critical for end users to have access to the data they need to make decisions. Zeeco offers a number of products, services, and solutions to help our customers understand equipment performance, monitor areas of concern, and make necessary improvements.
Transition to H2 and Other Renewables
Applying the proper expertise and experience, burning H2 in steam generation systems and other industrial burner applications can greatly reduce operating fuel costs while also helping to meet new carbon emissions regulations. Hear what our experts had to say about the transition to H2 fuels in our Thought Leadership Forum.
Transition to Hydrogen Fuels by...
Thought Leadership Forum: H2 Fuel & Emissions Reducing Burner Technology
As new GHG emissions regulations go into effect, and Zeeco is committed to providing resources, technology, and support to help companies comply. Play the YouTube video above to hear Zeeco experts explore hydrogen-fired burners, lowering NOx and CO emissions, and the latest advancements in burner technology.
Renewable Projects
With so much focus on reducing emissions, Zeeco is providing plants, facilities, and other operations with the tools necessary to reduce their carbon footprint.
See how Zeeco products are making a real-world impact toward a sustainable future.
VOC Emissions Control
Hydrocarbons are transported and stored multiple times throughout the production life cycle; even when idle in storage, changes in temperature and pressure will generate VOCs. Zeeco’s activated carbon adsorption vapor recovery units recover some or all of those hydrocarbons as a liquid that can be returned as a valuable product instead of lost during combustion or as a fugitive emission—without producing any thermal NOx.
Control VOCs with...
Extending equipment life
Technology Developed for Space Improves Operations on Earth
We partnered with Emisshield® to utilize award-winning coatings technology developed for space to benefit fired equipment applications here on earth. Emisshield® water-based ceramic nano-emissive coatings extend the life and enhance the performance of fired equipment using a proprietary application process that changes the physics and thermodynamics of heat transfer of any surface.
Long-lasting equipment ensures proper performance over extended periods of time and limits shutdowns required for service and maintenance. And with improved overall temperature uniformity, efficient, effective combustion is easier to achieve and maintain.
Extend the life of your equipment with...
Custom Engineered Solutions
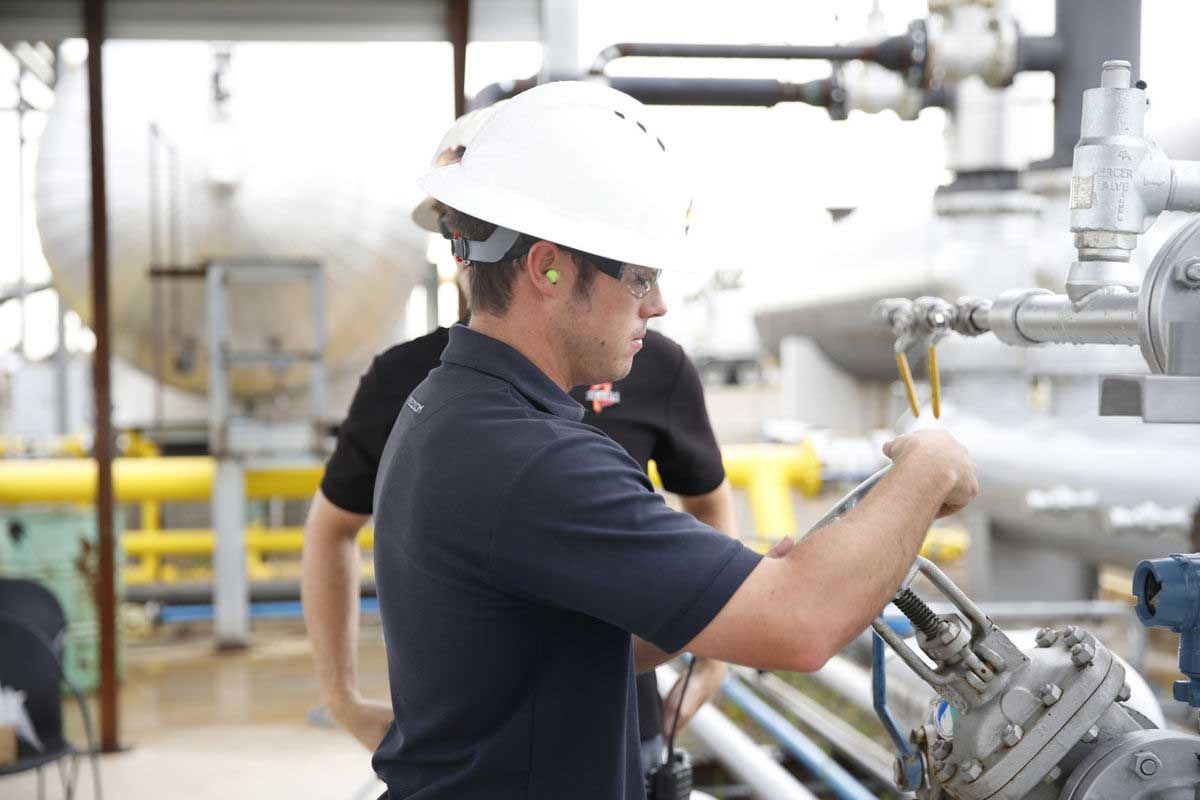
High Emissivity Coatings
Flare Tip Drone Inspections
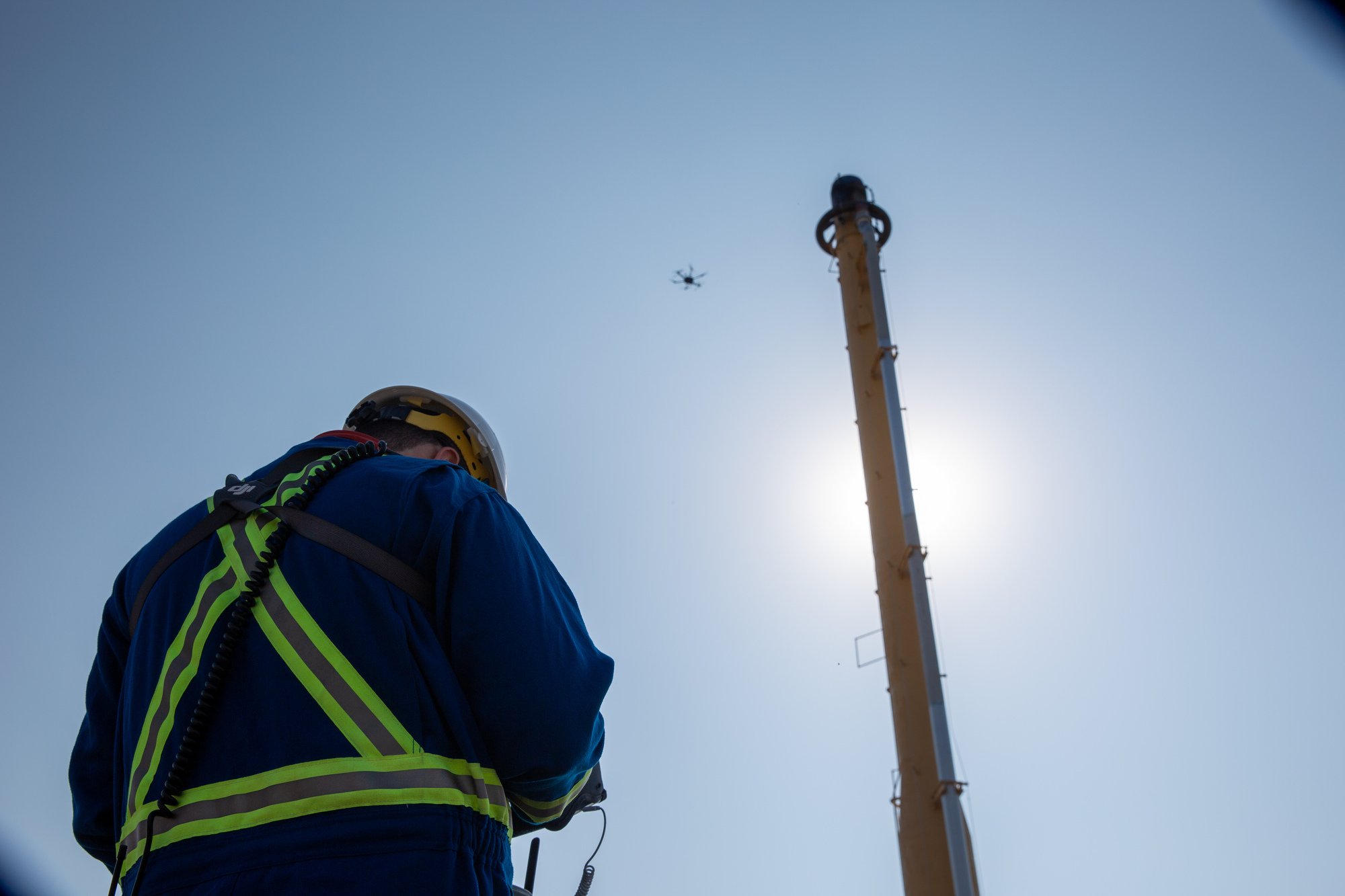
Minimizing Global Travel
Addressing environmental issues means utilizing fewer resources to accomplish our goals. By employing immersive technologies, such as our Global Bridge AR field kit, to serve customers in remote facilities, we can mitigate the need for global travel and reduce the carbon footprint of our business operations.
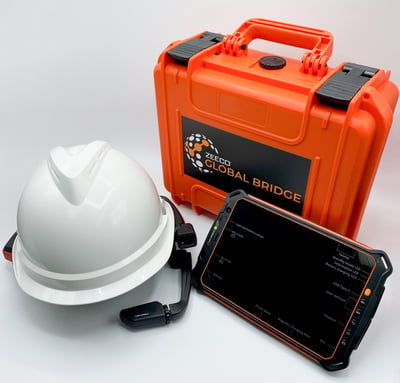