
Smokeless
Advanced designs to promote complete, efficient combustion
air
Zeeco offers several air-assisted flares using our advanced designs to promote complete, efficient combustion of heavier waste gases at sites where steam is not available or economical. Air-assisted flares use blowers to inject assist air directly into the waste gas stream as it exits the tip, resulting in smokeless burning and long flare tip life.
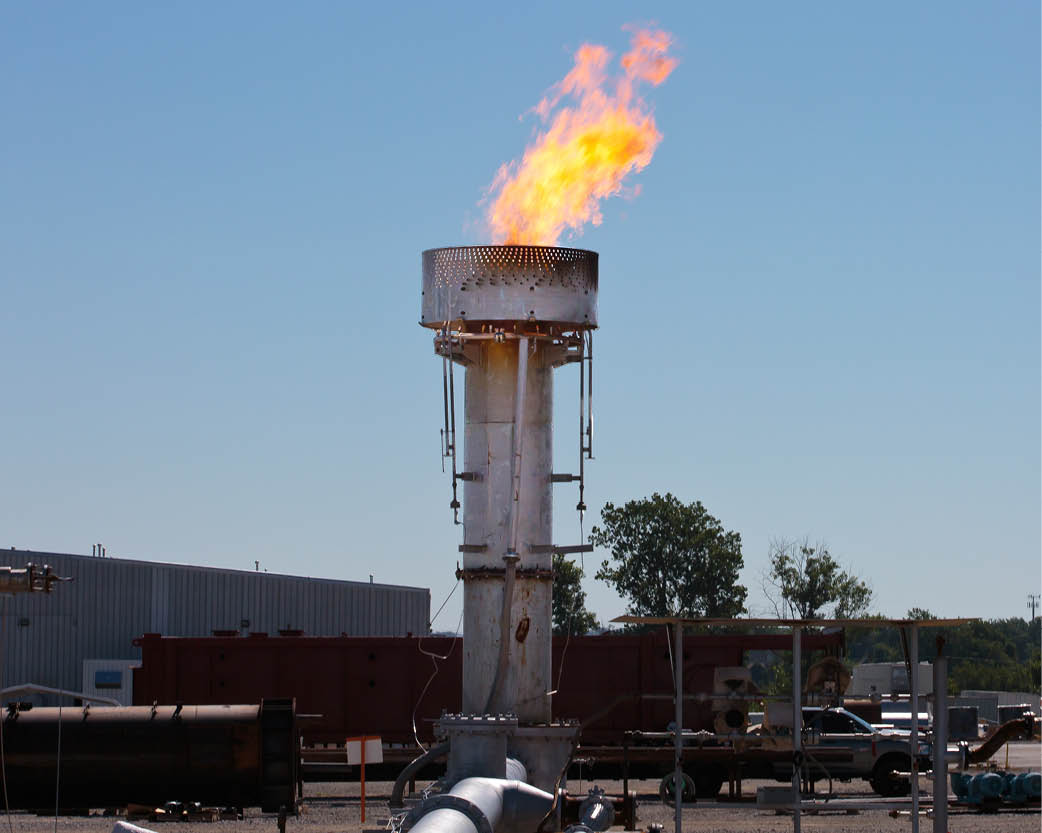
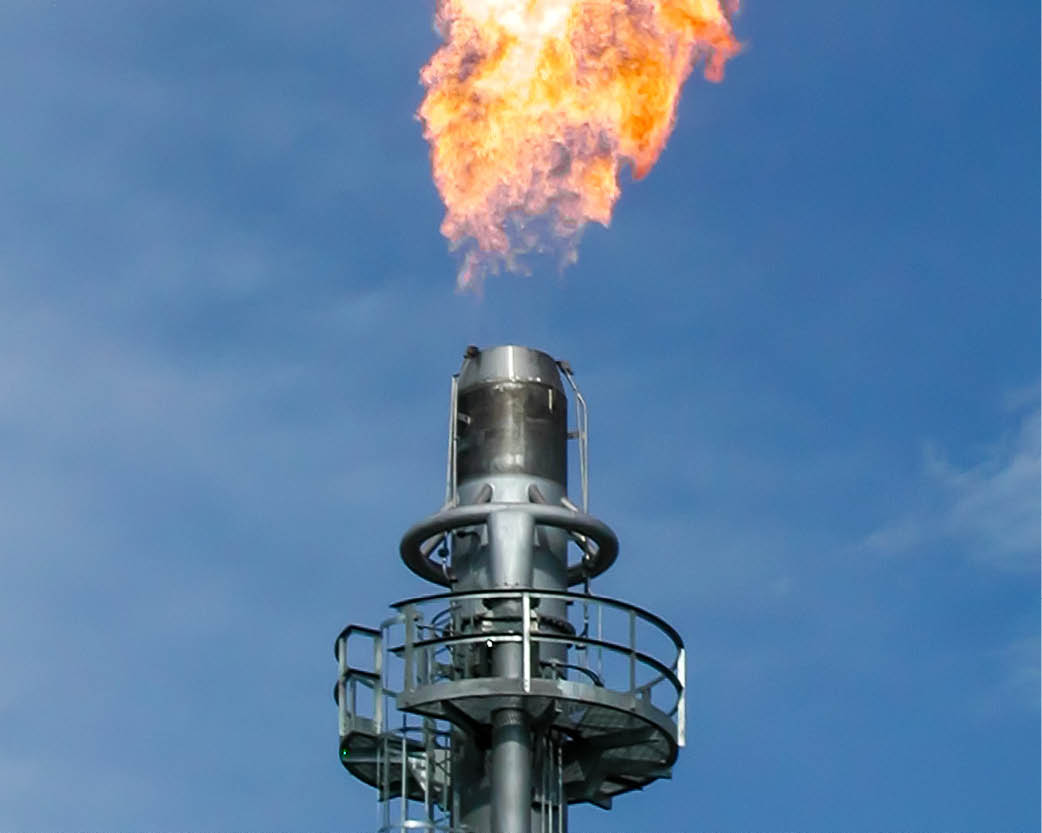
AF
When smokeless flaring is desired and neither steam nor assist gas is available, blowers can be used to inject combustion air directly into the waste gas stream as it exits the flare tip. The ZEECO AF air assisted flare tip incorporates a proprietary design that splits the waste gas stream into several smaller streams at the top of the flare to increase the gas / air contact surface area and promote better mixing. This key design feature maximizes the waste gas / assist air mixing while minimizing the amount of forced air required and resultant blower horsepower. Forced air from the blowers and gas from the flare header are routed separately from the base of the flare stack to the top of the flare. At no point do the air and gas mix prior to leaving the flare tip, ensuring the safety of the system. In addition, with this design concept, any ZEECO AF air assisted flare can operate without the blowers being on and provide for safe disposal of the waste gases in the event of a power outage. The Series AF flare tip produces a superior quality flame, which stays erect during all atmospheric and flow conditions. Flame lick on the exterior of the flare and burnback inside the flare tip, are virtually eliminated by the forced air from the blowers, which create a strong upward velocity, making the impact from the wind minimal in shaping or moving the flame. The forced air also shortens the flame length and reduces radiation at grade by ensuring a very aerated mixture at the exit of the flare tip.
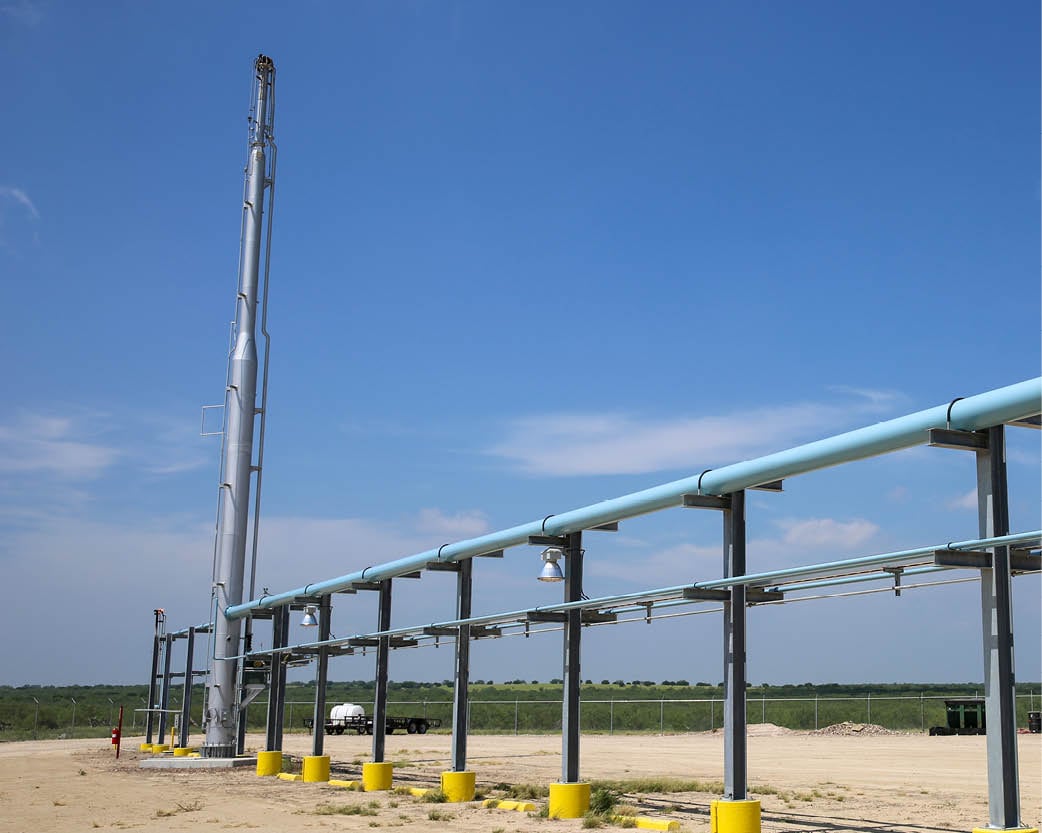
Ufaa
UFAA flare systems are used for applications where smokeless flaring is preferred for normal or low flow operation, and the gases being flared would produce smoke without some type of assist. This flare tip uses a small amount of air from a blower, located at grade, to produce smokeless burning and a clean flame for purge, normal, or low flow rate conditions. This system is typically used when the required smokeless flow rate is small compared to the possible maximum flow rate in the flare system.
Elevated Air Assisted Advantages:
- This system is used when other assist mediums, such as steam or assist gas, are either not available, not preferred or not economical.
- Air injected by a small blower produces smokeless burning with minimal requirements in horsepower and with minimal impact to the total capital cost of the flare system.
- The UFAA system is designed so it can be retrofitted to any existing non-smokeless utility type pipe flare tip assembly to achieve some level of smokeless performance.
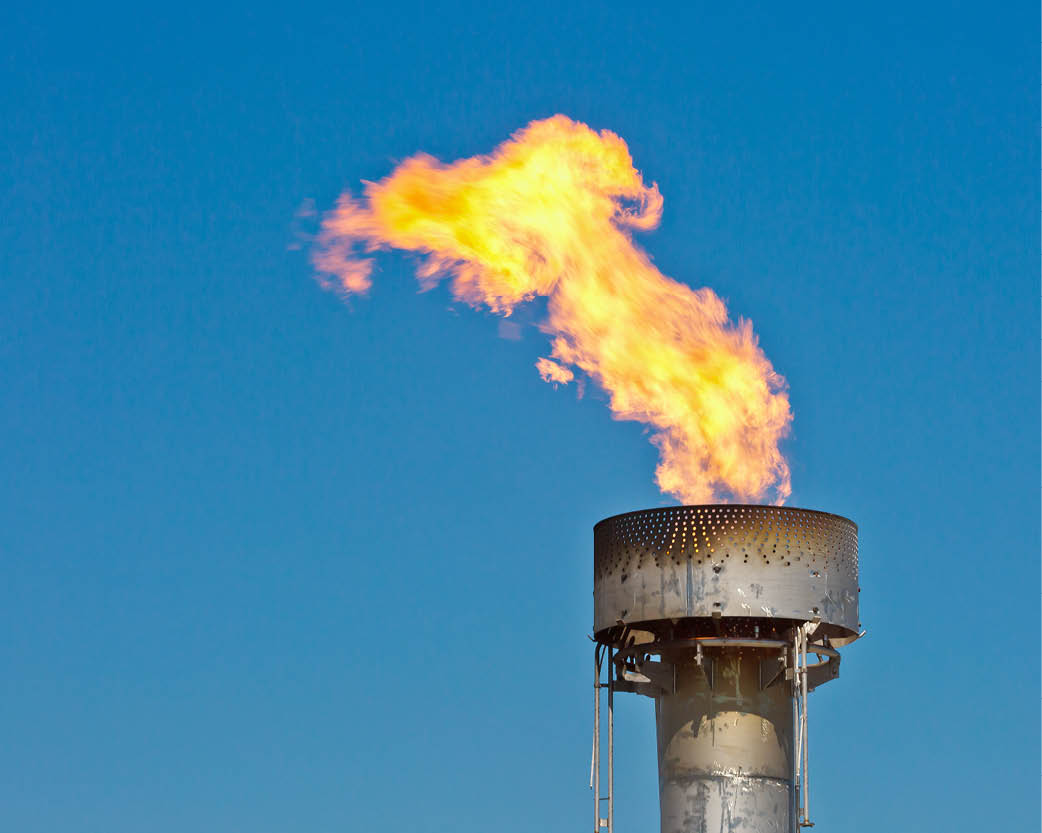
hpaas
Zeeco has exclusive rights to HPAAS flare tip technology. Aramco in Saudi Arabia developed and patented the HPAAS flare tip technology, and Zeeco is the exclusive licensee for the worldwide sale and production of the HPAAS flare tip technology. The HPAAS flare tip assembly is specifically designed for applications where water is scarce or the cost of steam is high. This system produces smokeless burning of saturated hydrocarbon flare gas streams that are the result of oil production, tank vapors, or continuous gas leakage from refining or production processes. Instead of steam, the HPAAS flare tip assembly uses air from a compressor to produce smokeless burning.
HPAAS Advantages
- The air requirement is very low, and the use of compressed air means the air supply line on the flare stack is very small
- The system is well suited for retrofits to an existing non-smokeless flare system.
- Air injection creates smokeless burning, shapes the flare flame in the wind, prevents burn back on the flare tip assembly, and cools the flare tip shell, all resulting in a longer flare tip useful life.
Steam
Zeeco's steam-assisted flares are used in applications where heavier waste gases need to be disposed and high-pressure steam is readily available on site. Our proprietary flare designs offer exceptional smokeless performance, lower radiation levels, and less noise than typical air-assisted flares.
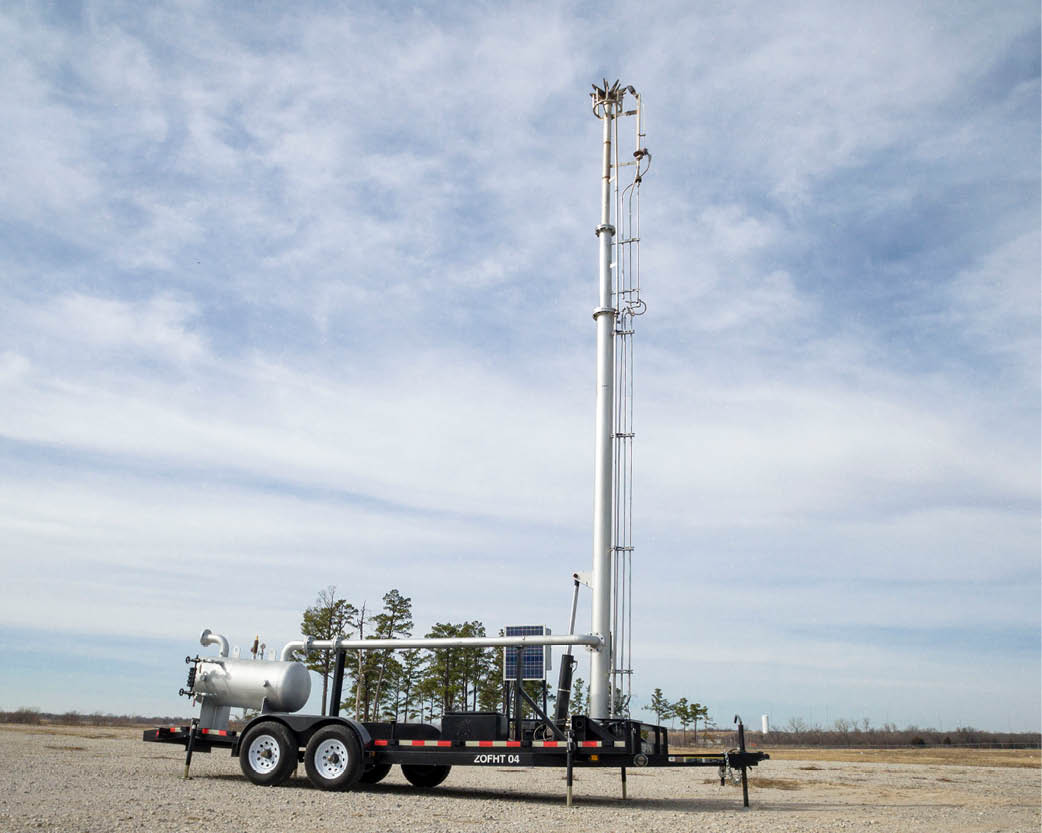
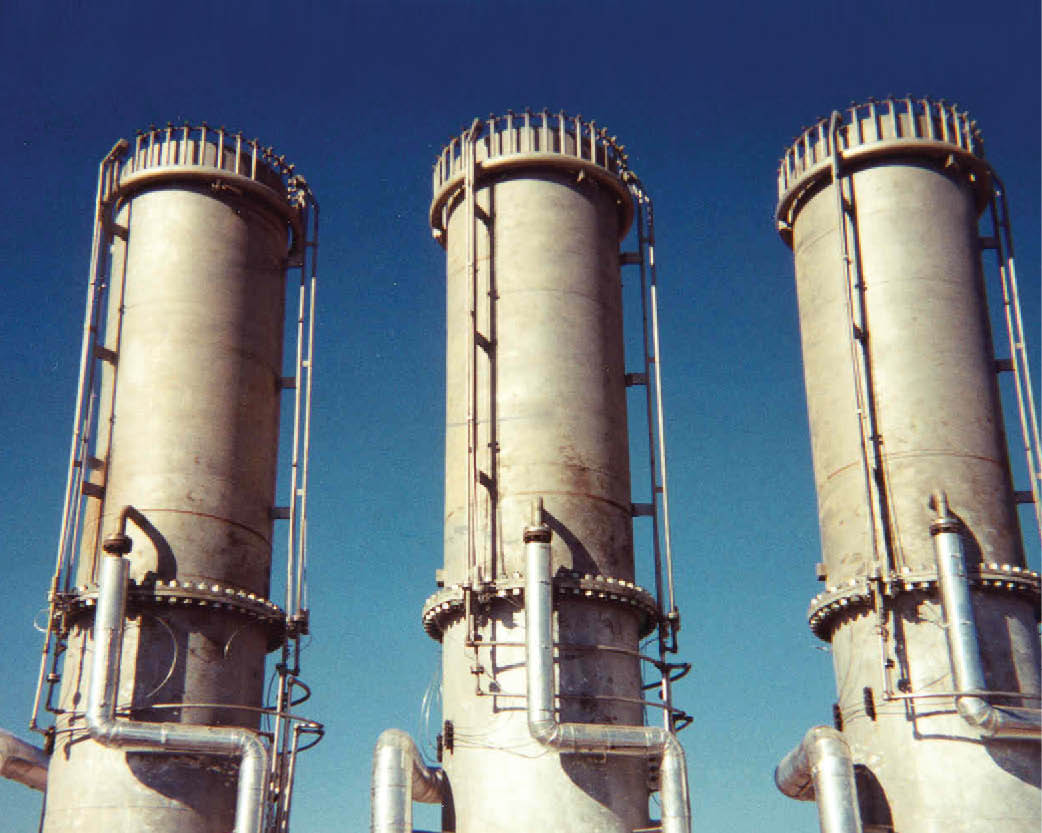
qFs
Zeeco’s QFS Steam Assisted flare tip provides control of smoke in a flare system at an affordable cost. The design of the QFS steam injection nozzle minimizes the noise associated with steam injection. The proprietary QFS steam nozzle is designed using a number of injection ports to successfully reduce the steam injection noise to well below that of conventional steam assisted flare tips. Injection of steam at the flare tip exit point provides more than smokeless performance. The steam also “shapes” the flare flame in high wind conditions, eliminating the downwind flame impingement seen on many non-assisted flare tips. The steam also assists in lowering the radiation level at grade, by lowering the emissivity of the flare flame, and by providing an upward vector to stand the flame up in a crosswind.
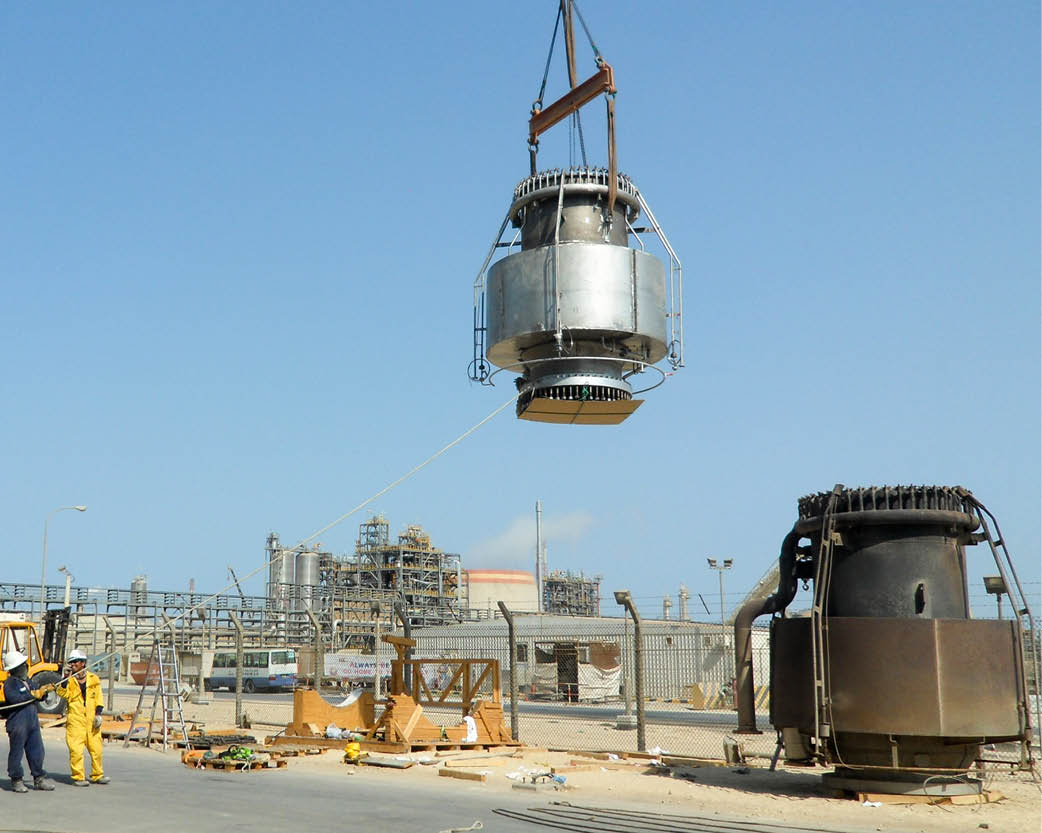
hcl
In Zeeco’s HCL flare tip design, the steam injection manifold is moved from the top of the flare tip to a point near the base of the flare tip. This moves the steam injection nozzles away from the heat of the flare flame, and into a position where a noise shroud can be added to muffle the jet noise from the steam injection. The HCL flare tip uses a system of internal steam / air tubes to route an air / steam mixture from the steam injection manifold up the interior of the flare tip and discharge this steam / air mixture directly into the gas column as it exits the flare tip. The steam and air mixture is injected directly into the flare gas at numerous points across the diameter of the flare tip, and not just from the perimeter as in most standard steam flare designs. The design of the steam injection nozzles and internal steam / air tubes ensures the highest possible steam efficiency in controlling smoke. The HCL flare tip design can reduce the required amount of steam for a particular smokeless rate by 35-40% below that required in a standard steam flare tip with upper steam injection only.
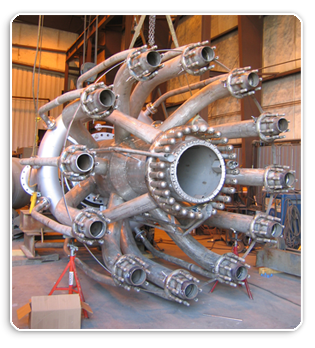
mjs
Zeeco’s Multi-Jet Steam Assisted flare tip assembly is used for smokeless burning of low pressure, heavy hydrocarbons. This Zeeco flare tip assembly is commonly used for applications associated with the flaring of low pressure or medium pressure gases from chemical plants and refineries. This type of flare tip is used for flaring gases such as acetylene, butadiene, butylene, xylene, and so forth.
Zeeco normally uses medium to low pressure steam as the assist medium to inspirate air, create turbulence, and produce smokeless burning in MJS systems. The benefits to this approach include:
- Our MJS flares divide flare gas into multiple small-diameter nozzles at the flare tip exit point, allowing for much better air accessibility.
- The smaller flames from these multiple nozzles and increased access to the surrounding air results in lower assist utility requirements and higher smokeless flow rates. This increases the efficiency of injecting assist steam for smokeless burning.
- This flare tip assembly has the ability to burn these very heavy gases smokelessly using the lowest possible steam assist quantities.
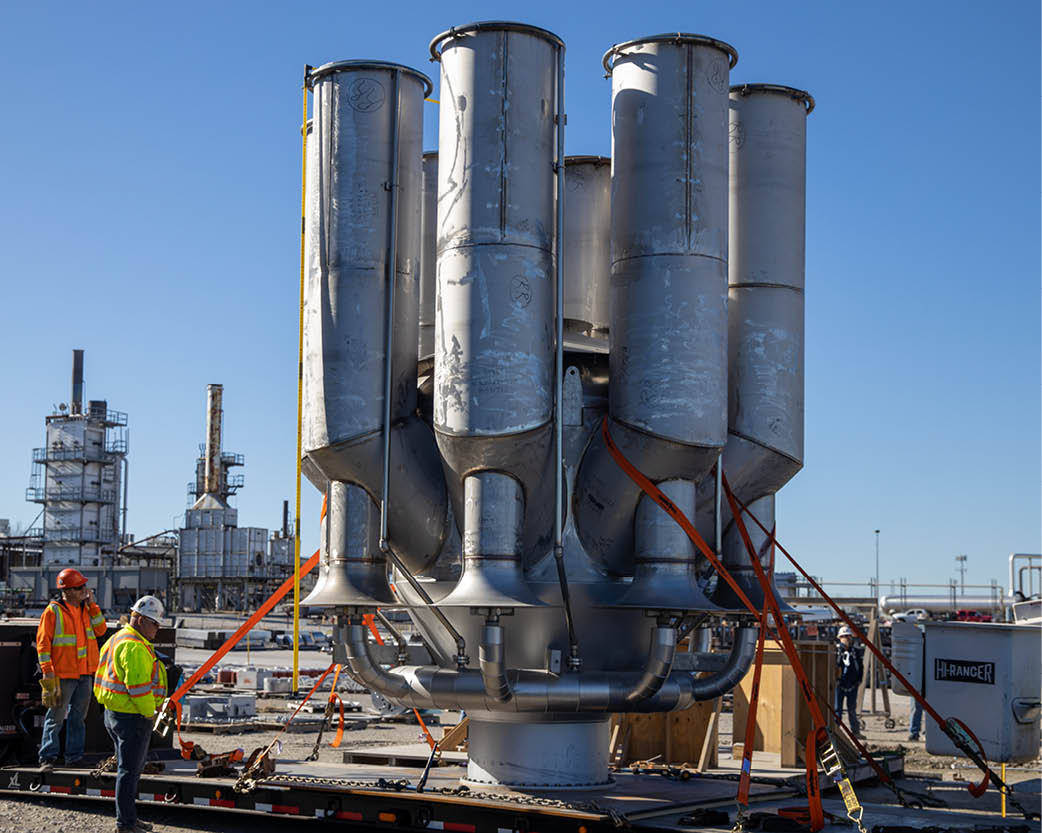
steamforce HC™
The ZEECO® SteamForce HC straight tube design achieves smokeless flaring with dramatically less steam consumption and no pre-mixing of air and fuel gas. SteamForce HC uses a true venturi design, significantly increasing the inherent efficiency and decreasing dependence on fuel gas pressure and high rates of steam to achieve smokeless combustion.
Less steam saves money and reduces emissions generated from the production of steam.
SteamForce HC solves the most challenging aspects of steam flaring today:
- Longer Flare Tip Life
- No Pre-Mixing Before Exiting the Flare Tip
- Reduced Emissions Through Dramatically Lower Steam Demands
- Lowest Cost of Operation
- Less Dependent on Fuel Gas Pressure for Smokeless Operation
Smokeless Operation at Lower Flow Rates
Given a flare gas pressure of 3 psig at maximum flare gas flow with smokeless operation at 20% of maximum flow, flare gas flow rate to achieve smokeless operation was a mere 0.12 psig – versus other designs which require flare gas pressures of up to 5 psig to achieve smokeless operation.
Revolutionary SteamForce HC Technology
The air and steam mixture leave the flare at the same elevation as the flare tip exit – no pre-mixing. Because other industry designs pre-mix the air and steam with the flare gas prior to exiting the flare tip, they are forced to operate at higher enriching rates to compensate.
The SteamForce HC maximizes the amount of air entrained by a given amount of steam. With more air flow, less purge steam is required to protect the equipment during low flow scenarios.
SteamForce HC improves flaring efficiency and reduces steam consumption while meeting EPA Code of Federal Regulations, Chapter 1, Subchapter C, Part 63, Subpart CC requirements – and can do so at lower steam and purge rates than any other competitive offering.
Zeeco’s SteamForce HC makes a dramatic difference for companies who want a lower cost of ownership, lower emissions, and a flexible design in a flare tip that will operate smokelessly with less steam at lower flow and purge rates than competitor offerings.
gas
Zeeco offers both single-point and multi-point gas-assisted flares for smokeless burning of low- pressure, heavy hydrocarbons. Our patented designs deliver stable burning, high-destruction efficiency and low radiation levels wherever steam or air is unavailable.
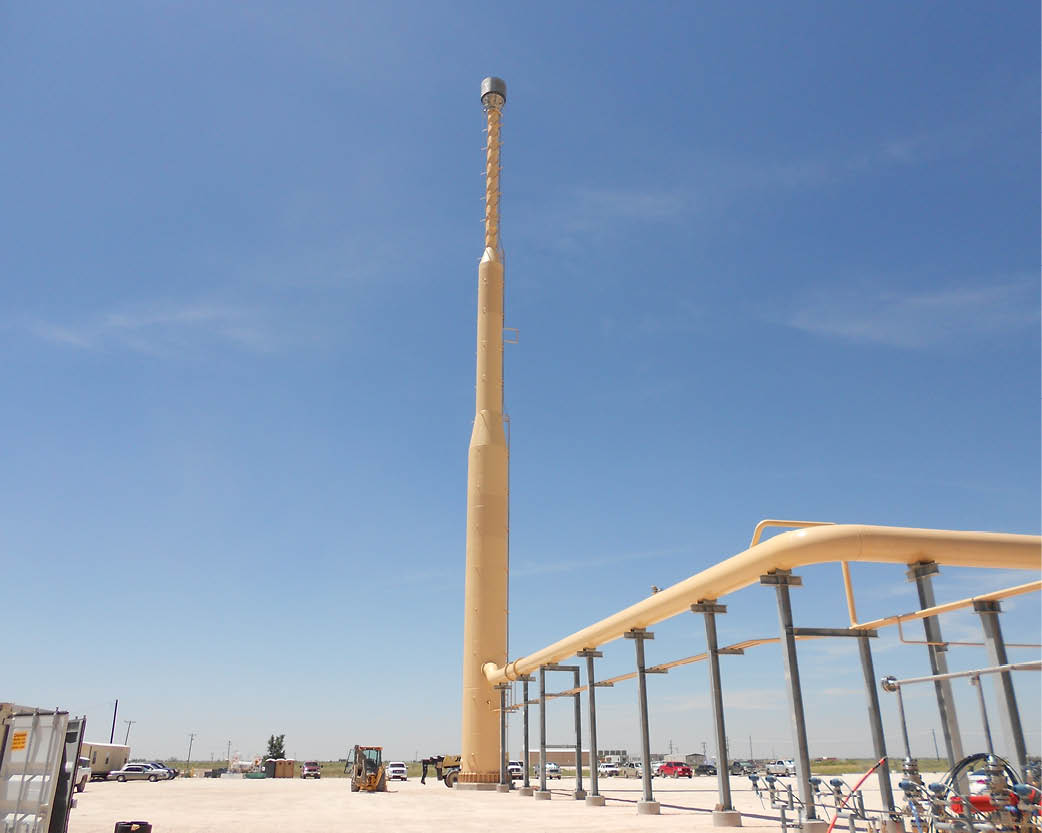
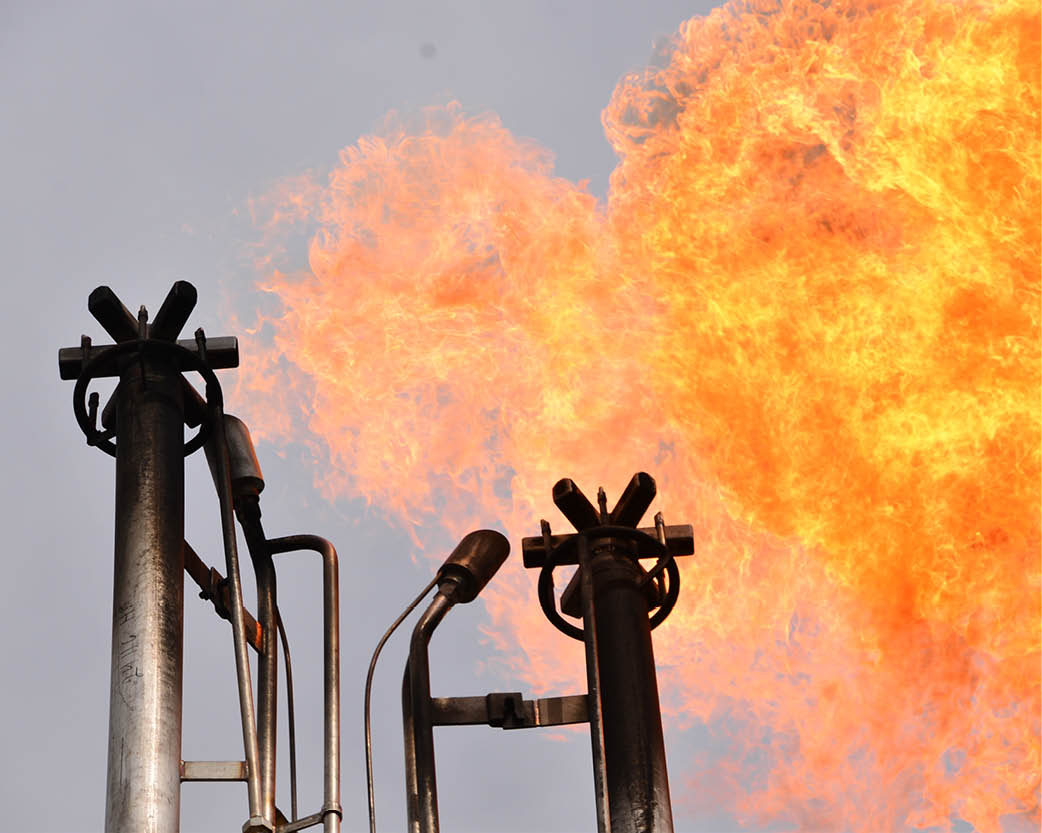
multi-jet Gas Assisted Flare System
Zeeco’s Multi-Jet Gas Assisted flare tip assembly is used for smokeless burning of low pressure, heavy hydrocarbons. This Zeeco flare tip assembly is commonly used for applications associated with the flaring of low pressure or medium pressure gases from separators for offshore and onshore production facilities. These facilities commonly have no steam available to use for smokeless burning of heavier hydrocarbon gases, necessitating the use of air assist or high pressure gas assist.
Zeeco normally uses high-pressure natural gas as the assist medium to inspirate air, create turbulence, and produce smokeless burning in MJGA systems. The benefits to this approach include:
- Our MJGA flares divide flare gas into multiple small-diameter nozzles at the flare tip exit point, allowing for much better air accessibility.
- The smaller flames from these multiple nozzles and increased access to the surrounding air results in lower assist utility requirements and higher smokeless flow rates. This increases the efficiency of injecting assist gas for smokeless burning.
Pressure
Zeeco's sonic flares are widely used in the oil and gas industry, both onshore and offshore. These flares employ high-pressure waste gases to achieve an extremely high destruction rate with superior smokeless performance and low radiation levels.
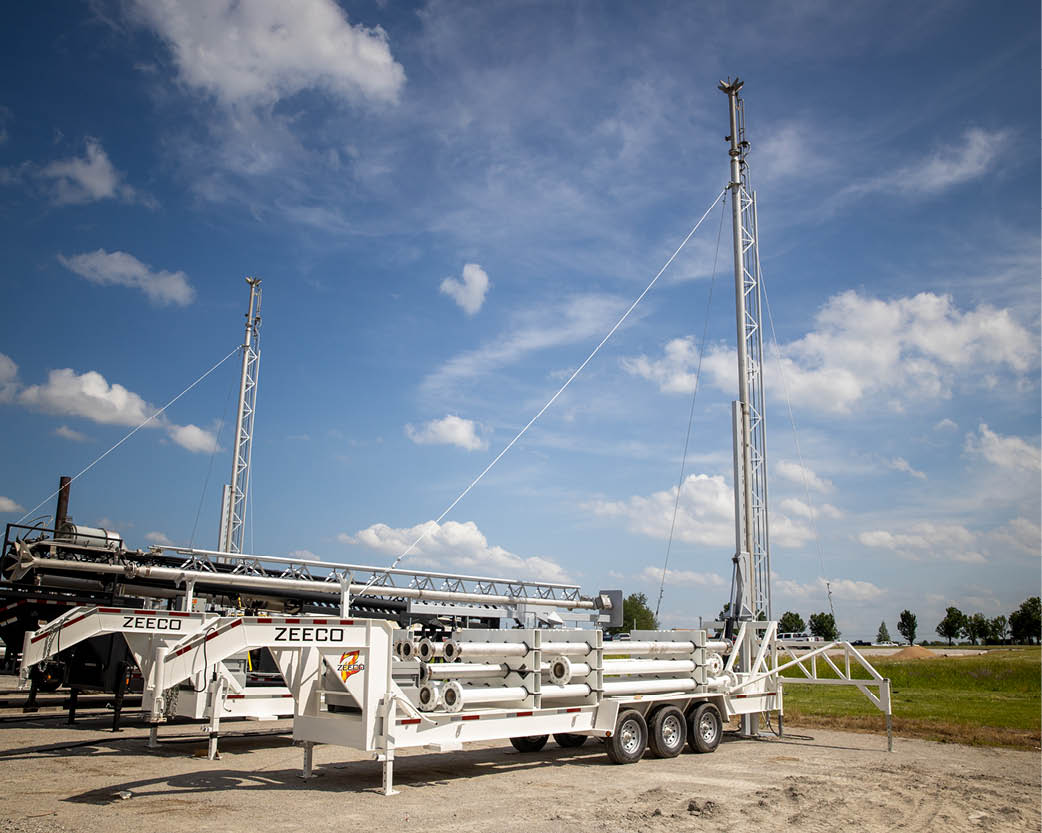
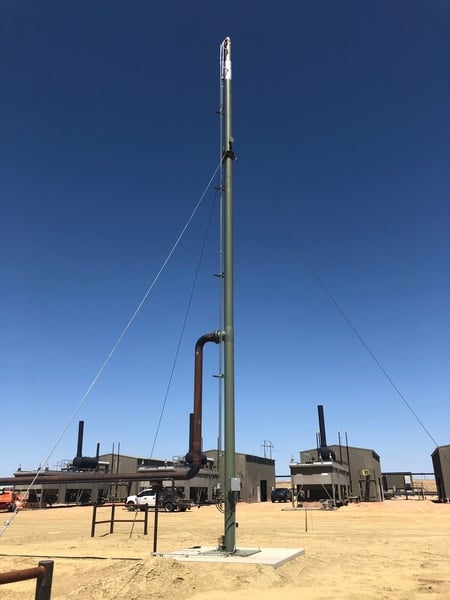
single-point
Single-Point Sonic flare systems are used primarily for applications in the oil and gas production industry, both onshore and offshore. They are also used in refining, chemical, and any other flaring situation where the flare system pressure is high enough to generate sonic velocity at the flare tip exit point.
Single-Point Sonic Advantages
- Single-Point sonic flare systems typically have non-assisted or steam assisted flare tips that have special stabilizers built into the flare tip exit point.
- These special stabilizers ensure the flare flame will not “lift-off.” Promoting a stable flame at the flare tip exit point also ensures a very high destruction efficiency.
- Single-Point sonic flare systems also ensure the flare tip diameter is kept as minimal as possible, thereby resulting in lower equipment and utility costs, a longer flare tip life, less flame pull down, and a smaller wind profile for structural forces on the stack or boom support system.
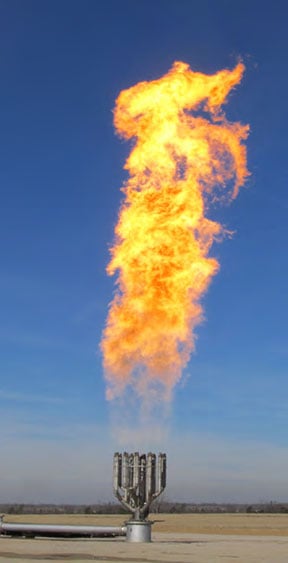
multi-jet Sonic Flare System
MJ (Multi-Jet) Sonic flare systems are used primarily for applications in the oil and gas production industry, both onshore and offshore. They are used where high flare gas pressures are available (15 psig and up) and the customer prefers to have some smokeless burning capability and also lower radiation levels. Zeeco can design Multi-Jet flare tip assemblies with either a fixed exit area or with a variable exit area. Variable exit area tips use a special high-reliability spring force system to reduce the exit flow area at lower flare header pressure levels.
MJ Advantages
- Designed specifically to ensure high stability and high destruction efficiency, even with sonic velocity at the tip exit point.
- The flare tip has many smaller diameter exit nozzles, resulting in a much larger flare gas to ambient air contact surface and much higher air inspiration volumes and increased turbulence in the combustion zone.
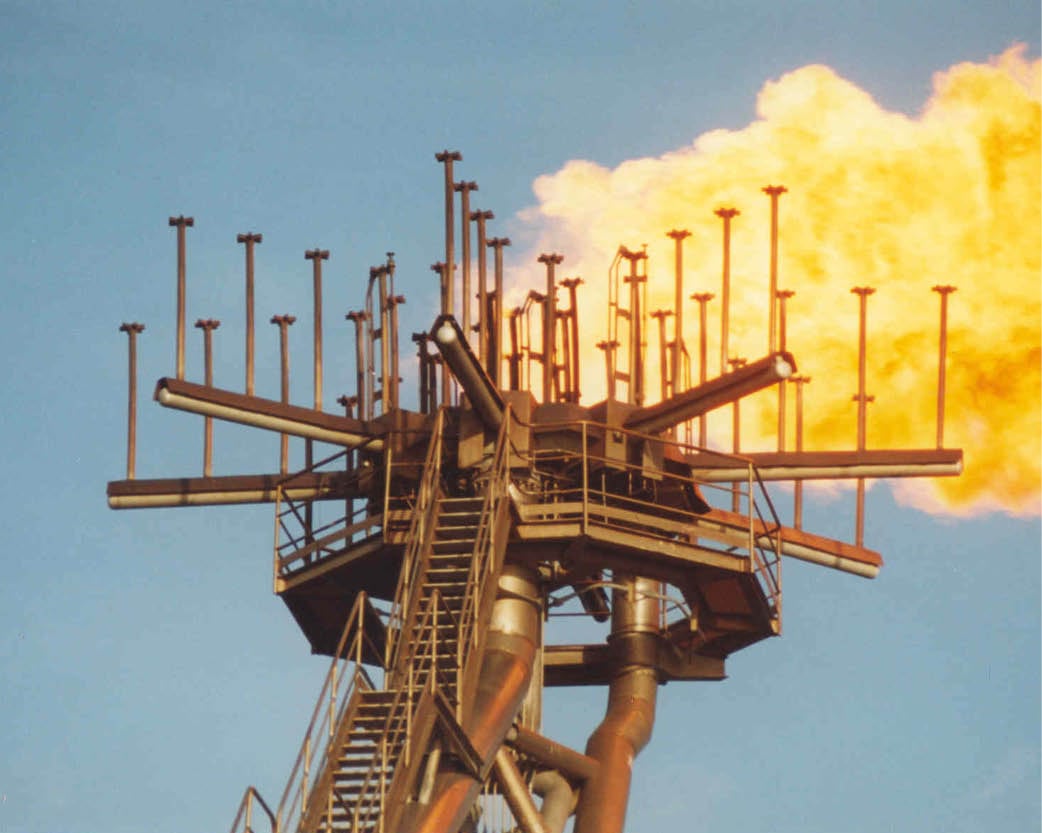
Staged multi-point
Zeeco's elevated staged multi-point flare is fed from a manifold which distributes the flow of flare gas to individual branches (stages) each containing one or more burner tips. Control valves direct the flow of flare gas to each stage based on upstream pressure.
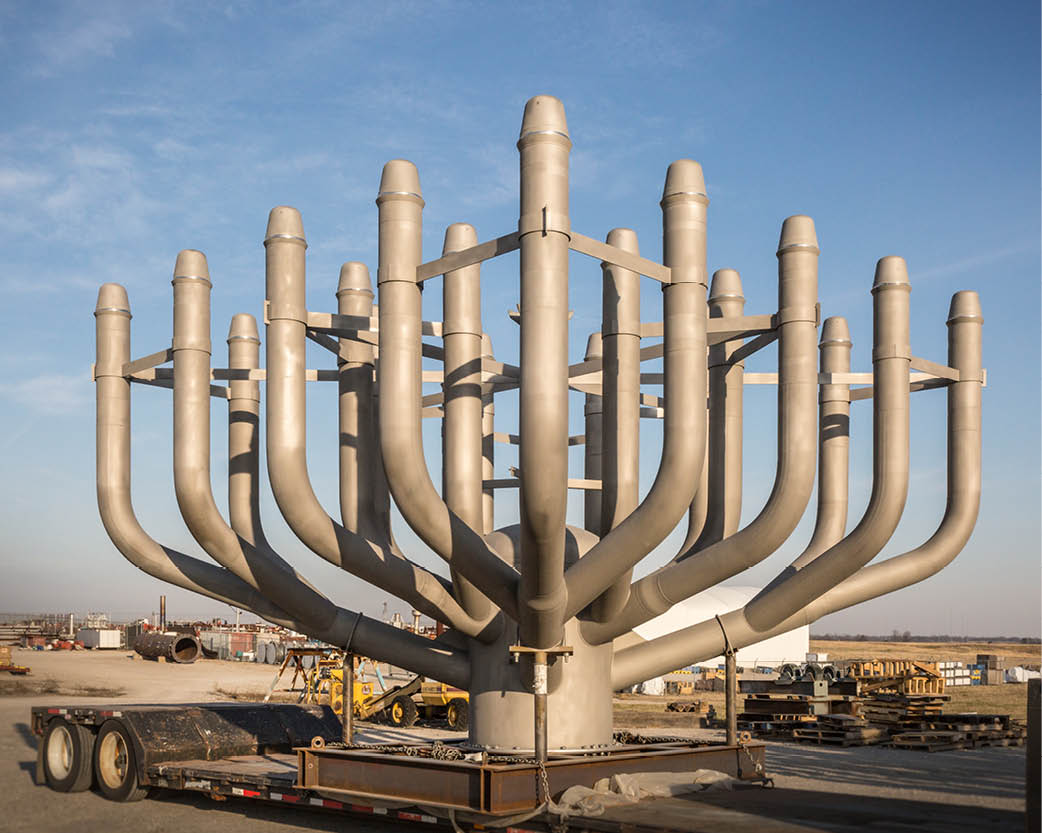
variable jet
The ZEECO® Variable Jet (VariJet) flare tips are high pressure tips that use the energy of a high pressure gas stream to improve smokeless performance. To enhance the tip's ability to capitalize on high exit velocities and superior mixing that result from high gas to air surface area ratios, each arm of the VariJet tip incorporates a self actuated variable exit area assembly that opens as necessary relative to internal pressure to ensure operation at high exit velocities over a wide range of flow rates. By operating at a high exit velocity, the flare does not require any additional assist media such as steam or air to operate smokelessly, even at low flow rates. This type of flare tip gives the normal benefits of a high pressure sonic flare, such as well defined and erect flame patterns and low fractions of heat radiated over a much wider range of flows; which leads to lower radiation levels on platforms and at ground level.
The operation of the VariJet is controlled by the incoming flare gas pressure that causes the exit area to vary, thereby providing a constant backpressure and high exit velocity across the full operating range. Through the utilization of varying exit area, purge gas requirements for the VariJet are the lowest of any flare type. Additionally, using this technology allows the VariJet to be mounted and function well when firing at an angle or even horizontally.
Applications
- Offshore and onshore oil and gas production, gas compression facilities, gas pipelines, LNG process plants, grassroots petrochemical/olefins/polyolefins facilities
Advantages
- High stability, low fuel consumption pilots are standard
- 98.5% or higher hydrocarbon destruction efficiency
- Superior materials and construction features
- Non-assisted smokeless operation
- Low radiation levels
- Liquid carryover flaring requirements
- Mixed phase discharge capability
- Smaller knockout drums and piping
- Very large gas capacities with high smokeless requirements
- Shorter flame length
liquid
Some processing applications must dispose of off-specification, excess, or production liquids. Liquid Flares are a safe and effective method for disposing of this waste.
Applications
Liquid Flare systems operate to dispose of wastes from the following applications:
- Production well testing
- LNG plants
- Flare system knockout drums
- Lubricating fluids
- Pipelines
- Other applications
Flare Types
Zeeco designs liquid flares for both smokeless and non-smokeless waste fluid combustion. Smokeless flares require specialty systems designed to use either an outside source or utility to achieve smokeless burning (such as steam, air, gases, or water). The smokeless system may also utilize high pressure in the incoming fluid stream to atomize the wastes and promote smokeless combustion. Zeeco’s staff members have extensive experience in design, fabrication, and operation of Liquid Flare systems. Put our experience to work for you!
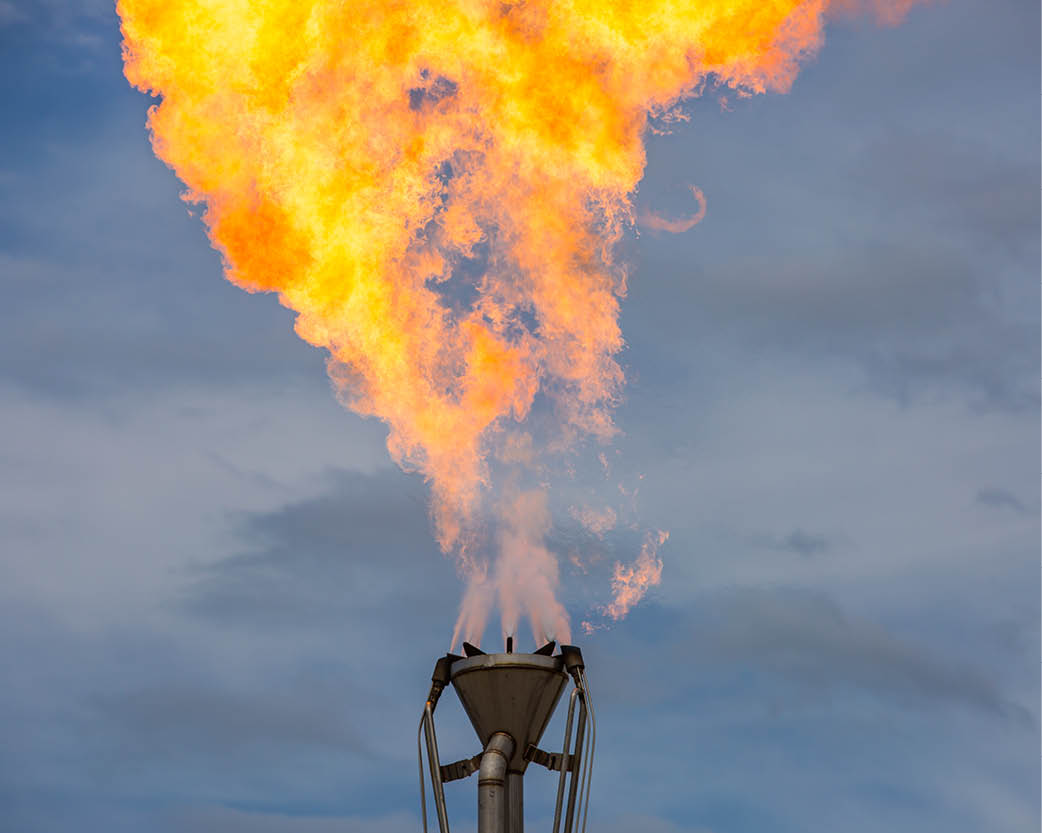
Services we offer
MARKETS WE SERVE
Zeeco can provide combustion and emissions control solutions wherever hydrocarbon processing takes place. Customers can find our equipment and services in upstream, midstream, and downstream oil and energy processes.
We also offer products and support for other industries and applications such as tank/terminal loading and storage, pharmaceutical, carbon black, pulp & paper, steel, food processing, and more.