
Thermal Oxidizers
Thermal Oxidizers, Incineration Systems, Waste Heat Recovery, and more
sulfur
A Sulfur Recovery Unit (SRU) uses the industry-standard Claus Process to recover elemental sulfur (also known as "sulphur") from gaseous hydrogen sulfide that comes with refining crude oil, and other by-product gases that originate from refining and natural gas processing. An SRU also reduces the hazardous sulfur emissions to limits permitted by national and local air quality requirements. Zeeco engineers all of the combustion systems used in SRUs.
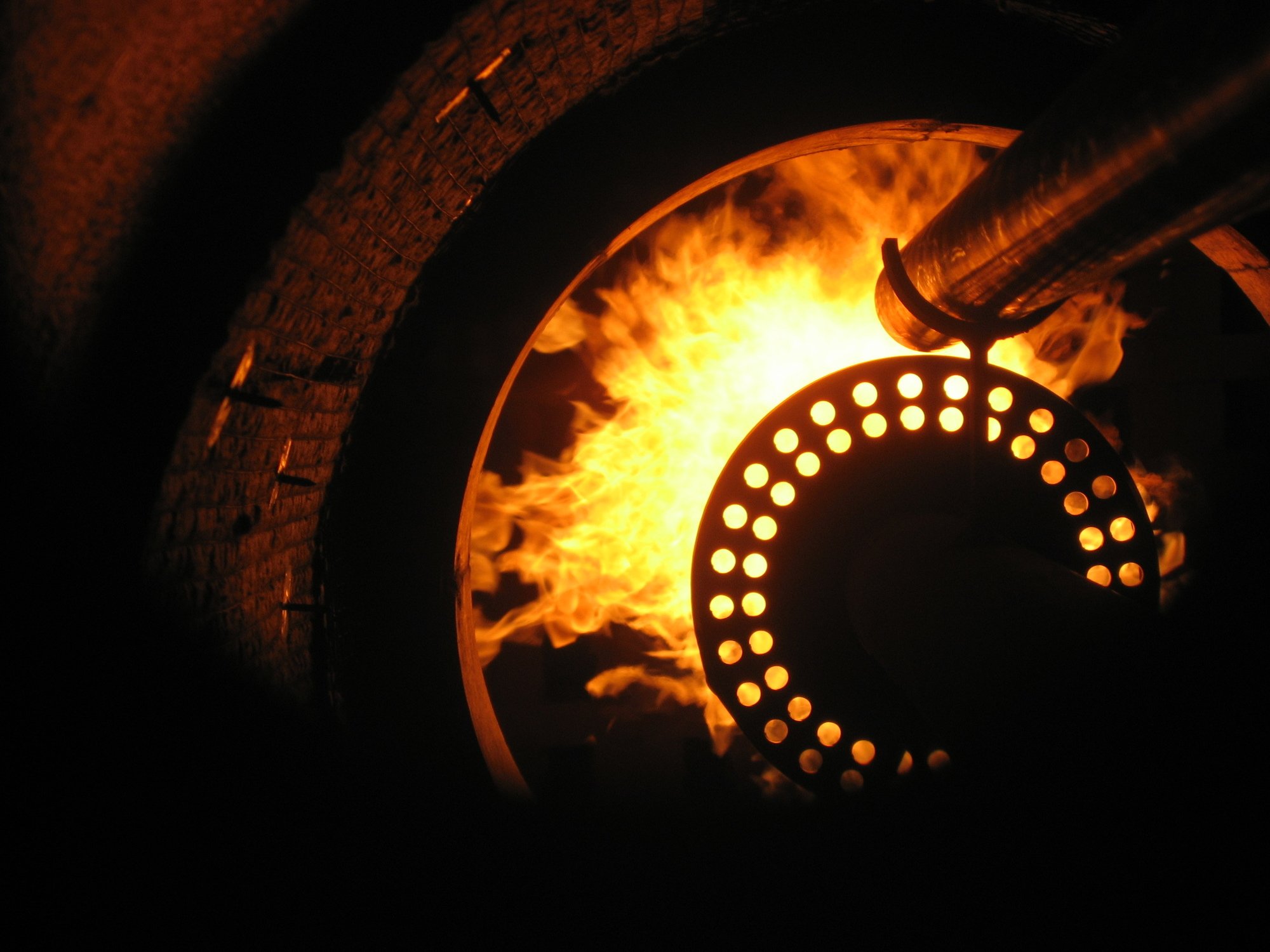
Sulfur Recovery Unit: Thermal Oxidizers
Thermally treating waste matter is a primary method for disposing hazardous & non-hazardous materials worldwide—it’s safe & effective. Zeeco offers a complete line of vapor & liquid thermal
ProFlame+ SRU Flame Scanner
The ZEECO® ProFlame+SRUTM Integrated Flame Scanner was specifically designed to provide reliable flame detection and superior background flame discrimination in SRUs.
Gas Processing Applications
Zeeco can supply a thermal oxidizer for any gas plant application, including amine treater acid gas, glycol dehydration (BTEX) off gas, and Sulfur Recovery Unit (SRU) tail gas.
SRU Combustion Equipment
The Sulfur Recovery Unit (SRU) is often referred to as the Claus Process. This process recovers elemental sulfur from petroleum & natural gas refining processes & reduces the hazardous sulfur
speciality thermal oxidizers
Incineration is a thermal process for converting waste gases or liquids to an environmentally acceptable condition. Our systems are capable of achieving 99.9999% destruction efficiency. The basic incineration system is comprised of an auxiliary fuel burner, a refractory-lined chamber, a discharge vent stack, and a control system. These components are described below.
Auxiliary Fuel Burner
This burner is provided to maintain the system operating temperature at the level necessary to achieve the desired performance. The burner can be fired with either gaseous or liquid fuel. The burner design is an integral portion of the incineration system design to provide the proper heat release profile and flame envelope to assure proper destruction of the waste gases or liquids.
Refractory Lined Chamber
Waste gas or waste liquid incineration requires that the incoming waste be treated (1) at a high temperature (typically 1200 to 2000°F), (2) for a minimum residence time (typically 0.5 to 2.0 seconds) and (3) in an environment to ensure proper turbulent mixing of fuel, air, and waste. To meet these requirements, a steel vessel lined with high temperature refractory is provided. The vessel size and refractory materials are selected to be compatible with the waste stream and to meet the basic time, temperature, and turbulence requirement.
Discharge Vent Stack
A vent stack transports the flue gas exiting the incinerator to the atmosphere. The vent stack height is fixed by flue gas dispersion requirements to avoid interference with other plant structures or operations. Vent stacks available separately.
Control System
An automatic control system is an integral portion of each incinerator. The control system assures that the unit will be operated in a safe manner to protect both personnel and equipment. To meet performance objectives, the waste combustion is performed under controlled and repeatable conditions. Typically, the control system monitors and actively controls flue gas temperatures, combustion/quench air flows, fuel pressures/flow, and flame stability to ensure safe and consistent equipment operation.
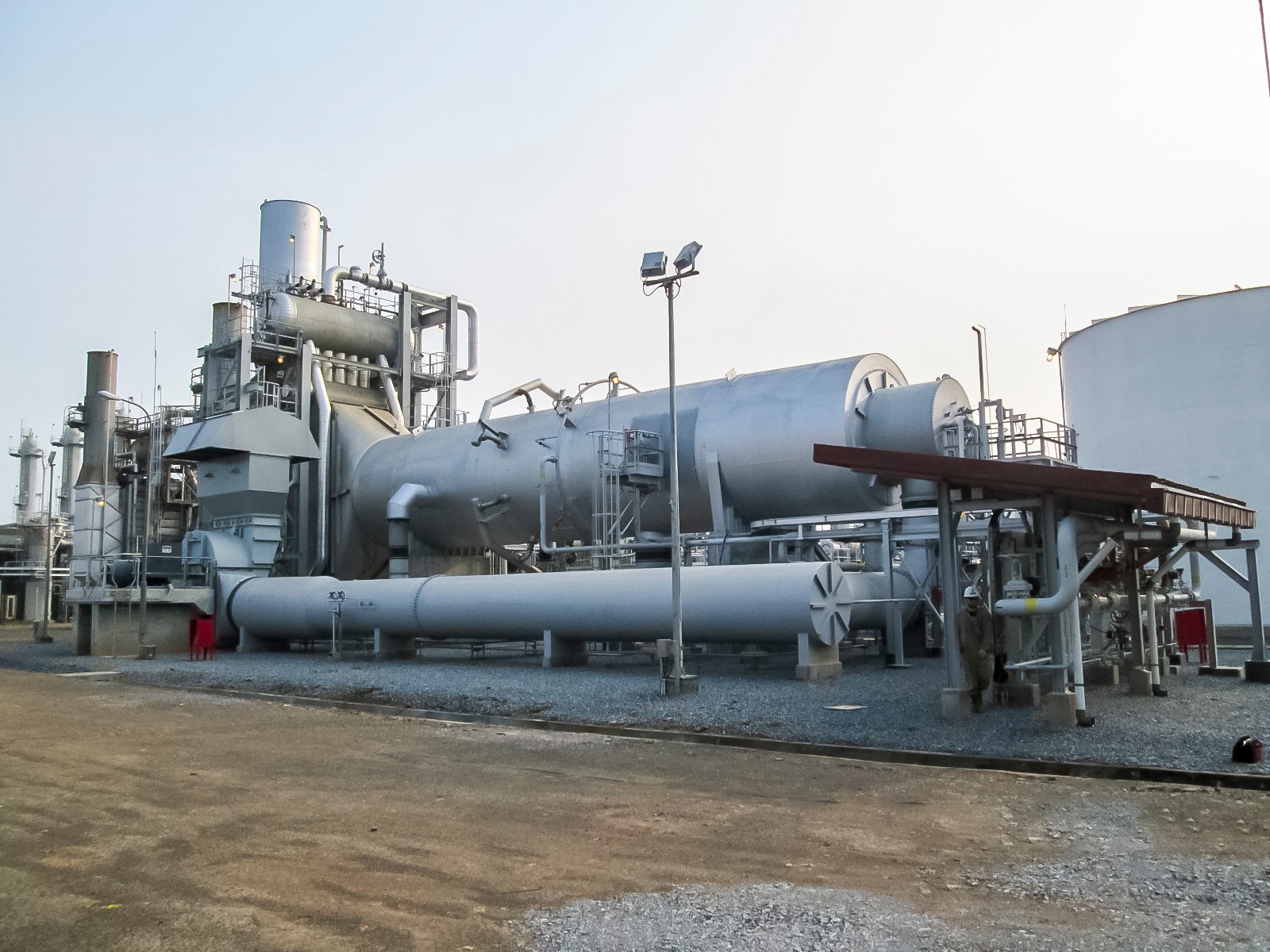
Halogenated Hydrocarbon Thermal Oxidizer
Halogen-based wastes are an unavoidable reality of the petrochemical and plastics industries.
ProFlame+ SRU Flame Scanner
The ZEECO® ProFlame+SRUTM Integrated Flame Scanner was specifically designed to provide reliable flame detection and superior background flame discrimination in SRUs.
Downfired Salt Thermal Oxidizer
Zeeco is the company to trust for Downfired Salt Thermal Oxidation Systems. Our engineers have decades of experience in designing these systems for petrochemical plants around the globe, helping
Carbon Monoxide Thermal Oxidizer
As a worldwide leader in thermal oxidizer solutions, Zeeco is the company to trust for your CO Boiler application. Our engineers have decades of experience in designing these systems for
Nitrogen Bearing Waste
Zeeco is the world leader in ultra low-NOx combustion solutions. For decades, our engineers have custom- designed Nitrogen Bearing Waste Thermal Oxidizers for petrochemical plants, petroleum
Gas Processing Applications
Zeeco can supply a thermal oxidizer for any gas plant application, including amine treater acid gas, glycol dehydration (BTEX) off gas, and Sulfur Recovery Unit (SRU) tail gas.
Regenerative Thermal Oxidizers
Regenerative Thermal Oxidizers (RTO) are a cost-effective solution for destroying volatile organic compounds (VOCs) through a thermal reaction and heat recovery process in high-temperature environments. Thermal ceramic beds are utilized in RTOs to recover heat from hot flue gas, which is used to preheat the incoming waste gas prior to the combustion chamber, minimizing the amount of fuel gas required to achieve high destruction efficiency (DRE). The cooled flue gas can then be safely vented into the atmosphere, limiting the carbon footprint and overall environmental effects.
Zeeco offers a variety of RTO solutions to fit your specific emissions needs, from standardized designs to fully custom solutions. We offer two–and three-chamber designs with implemented controls to ensure smooth cycling between ceramic beds for consistent preheating of the inlet waste gas. These configurations allow us to guarantee a DRE of 99%. The heat recovery efficiency of Zeeco's system can reach more than 97%, and autothermal operation, which uses no fuel gas, is obtainable under many waste gas characteristics.
Benefits
- Low Operating Cost
- High Flow Capacity
- Modular Design for Ease of Installation and Shipping
Design Considerations
- Optimal Waste Concentration
- Lower Explosive Limit
- Destruction Removal Efficiency (DRE)
- Emission Limits
- Utilities Available
- Plot Space
Available Equipment
- Thermal Ceramic Materials
- Electric Heater
- Flow Transfer Valves - Poppet/Butterfly
- Hot Gas Bypass
- System Bypass
- Waste Gas Pre-Treating and Post-Treating
- LEL Monitoring System
- Blowers (Process, Combustion, Purge, and Bypass)
- Integrated Controls
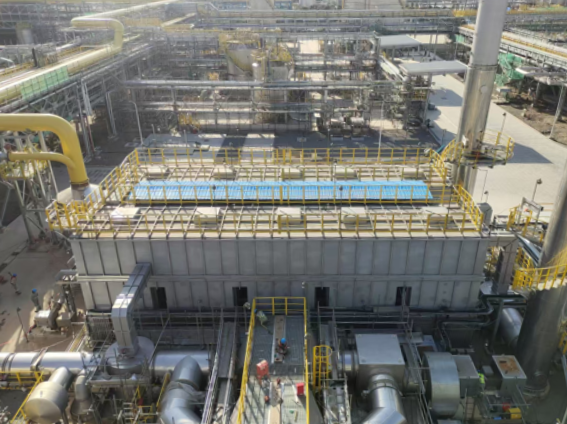
Packaged Incineration Systems
Zeeco’s packaged thermal oxidizers are available off the shelf or for rental applications, and can be delivered in as fast as a week. Mounted on a prepiped, prewired skid, our units require only minimal field assembly for fast installation. Quick response, on-site engineering, 24/7 support, and technical consultation are always available, even after installation.
Design Features
- ZEECO burner specifically designed for acid gas, glycol vent gas, flash gas
- ZEECO Burner Management System (BMS) PLC, instruments, controls, and HMI at local control panel
- Combustion air blower with variable frequency drive
- Full rain shield prevents acid gas condensation
- Greater than 99.999% DRE
- NFPA 86 compliance
Options Available
- Detonation arrestor
- Knockout drum
- Waste block valves
- Process control system (minimal outside control interface required)
- ZEECO Guardian™ Wireless Remote Monitoring System (cellular accessibility)
- Ladders and platforms
- ZEECO ultra-low NOx burners
Turnkey and Modularized Systems
With a Zeeco Turnkey Solution, there are no contractual layers between the customer, the OEM supplier, and the contractors.
Packaged Thermal Oxidizers for Gas Processing Applications
Zeeco designs and delivers the most reliable and efficient combustion and environmental solutions for gas processing applications.
AIR Heaters
A Direct Fired Air Heater effectively heats air, as needed in a variety of heating processes. This equipment is most commonly employed in Fluidized Catalytic Cracker (FCC) units in petroleum refineries. The direct-fired air heater is primarily intended to be used during start-up operations and short feed outages to heat the catalyst bed in the regenerator section of the FCC unit (catalyst regeneration). During normal operation, the air heater is not fired and air flows directly to the regenerator through the air heater without being heated. The mass flow rate and operating pressure during the un-fired condition may vary from that used during the fired case.
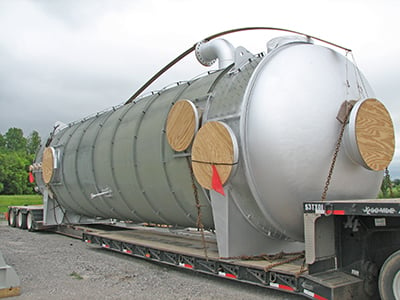
Direct Fired Air Heaters
Zeeco’s experienced engineering team goes the extra mile with each and every Direct Fired Air Heater.
Case Study: Retrofit of PDH Air Heater
In April 2020, duct burners failed in the propane dehydrogenation (PDH) air heater of Hengli Petrochemical Refinery located in Dalian, Liaoning, China – one of the largest refineries in China.
waste heat recovery
Waste heat recovery equipment reclaims heat from flue gas for use in other process units. The heat is transferred directly from the hot flue gas to a steam boiler or circulating thermal oil system. The quantity of flue gas and the associated exit gas temperature limit the amount of heat recovered. These systems can typically recover up to 70-80% of the theoretical heat available in the flue gas. System heat recovery ranges in size from 1.0 MM Btu/hr to 300MM Btu/hr.
A primary advantage of waste heat recovery is the production of usable heat without any additional fuel expense. Because the waste heat recovery equipment draws heat from flue gas that would normally be discharged to the atmosphere, all heat recovered can be utilized to offset the fuel required to produce process heat in other facility operations. Zeeco waste heat recovery equipment improves overall plant economics and plant efficiency.
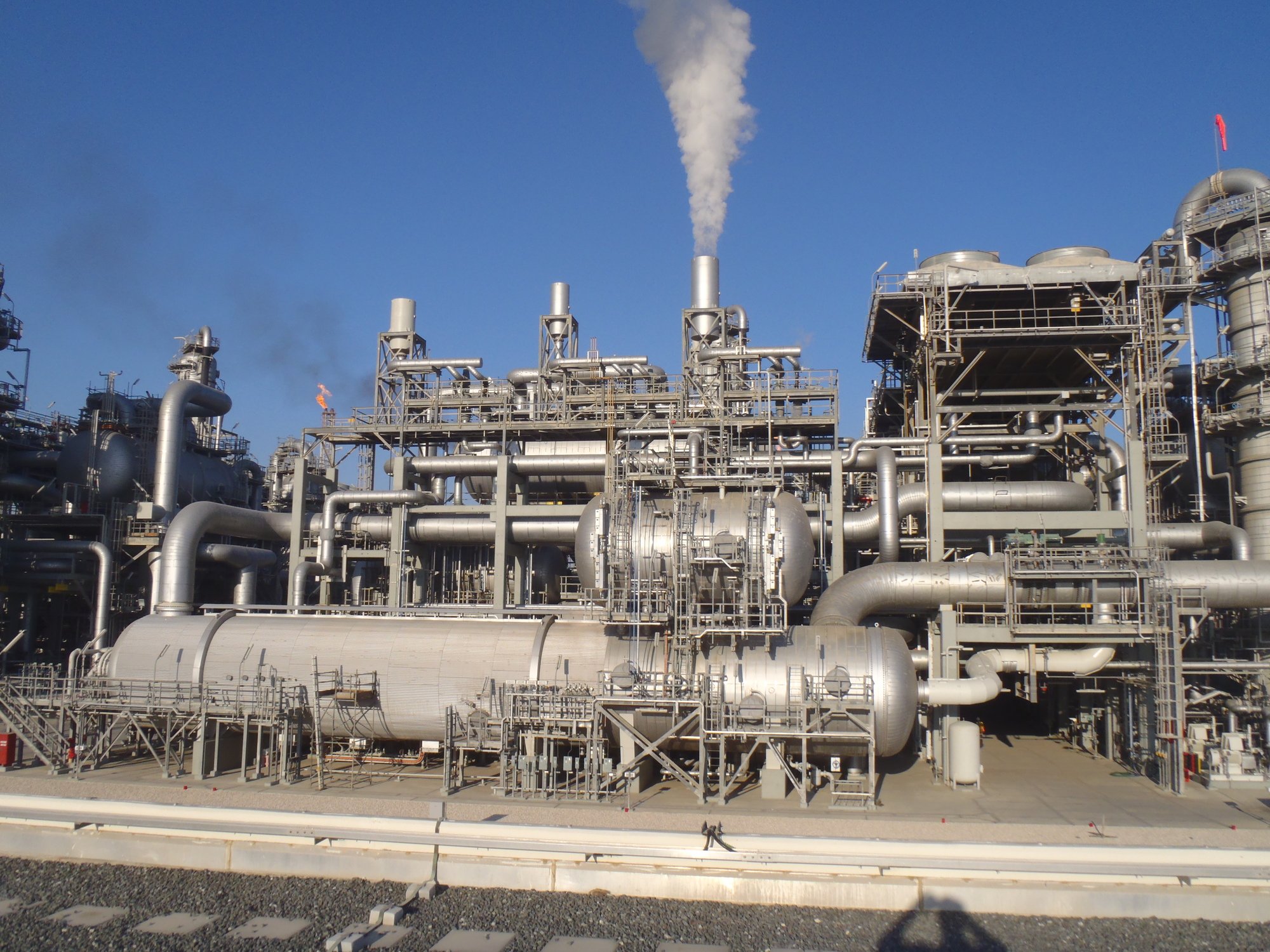
Turnkey and Modularized Systems
With a Zeeco Turnkey Solution, there are no contractual layers between the customer, the OEM supplier, and the contractors.
Nitrogen Bearing Waste
Zeeco is the world leader in ultra low-NOx combustion solutions. For decades, our engineers have custom- designed Nitrogen Bearing Waste Thermal Oxidizers for petrochemical plants, petroleum
Article: Thermal Oxidiser Waste Heat Recovery
Capturing the heat energy used for waste gas destruction enables processing plants to enhance their efficiency and minimise operating costs
Post-Combustion Treatment
The goal of any incineration or thermal oxidation process is to control the amount volatile organic compounds (VOCs) released to the environment. While these systems typically achieve high destruction of VOCs, additional air pollutants may be generated during combustion of certain compounds in the waste stream. If released to the atmosphere without further treatment, these compounds can form secondary air pollutants.
Zeeco provides a variety of proven, environmentally beneficial solutions for post combustion treatment. Depending on the application and the components of the flue gas, one or more devices can be incorporated to form a compact waste treatment system:
- Wet Scrubbers for HCI Removal
- Wet Scrubbers for SO2 Removal
- Baghouses (Fabric Filters) for Particulate Removal and Acid Gas Scrubbing
- Venturi Scrubbers for Particulate Removal and Acid Gas Scrubbing
- Selective Catalytic Reduction (SCR) for Post-Combustion NOx Removal
- Selective Noncatalytic Reduction (SNCR) for Post-Combustion NOx Removal
- Options for Catalytic Reduction of Dioxins and Furans
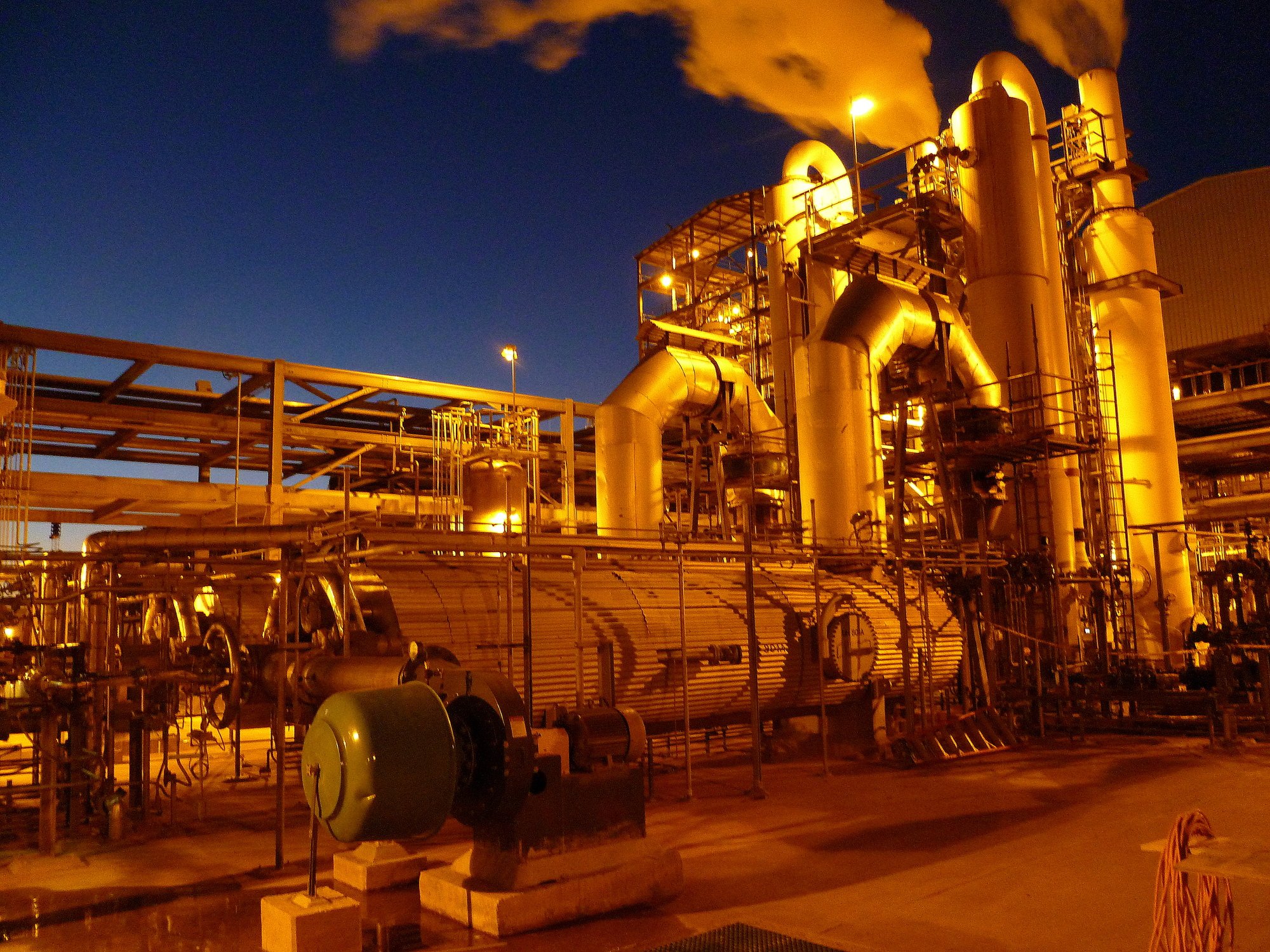
Vent Stacks
Vent Stacks are used to discharge gasses to the atmosphere at a safe and environmentally friendly elevation. The required elevation and discharge velocity is dictated by a variety of design parameters. These include the vent stack’s location and surrounding structures as well as the vent gas temperature, constituents, allowable ground level concentrations, odor threshold, corrosion requirements and structural integrity. Structural integrity should consider all possible live loads, earthquake and wind conditions.
Design Configurations:
- Single or double wall
- Self, derrick or guy wire supported
- Internal refractory lining or external insulation
- Carbon steel, alloy, fiberglass construction
- Strakes, tuned mass damper, or damping pad
- Retractable or fixed aircraft warning lights
- Rainshield material galvanized, aluminum, stainless
- Ladders and platforms
Design Codes:
- Any globally applicable design code, such as:
- ASME STS-1
- CICIND
- IS 6533
Additional Features:
- Custom thermal design to prevent corrosion
- Single or multiple piece lift configurations available
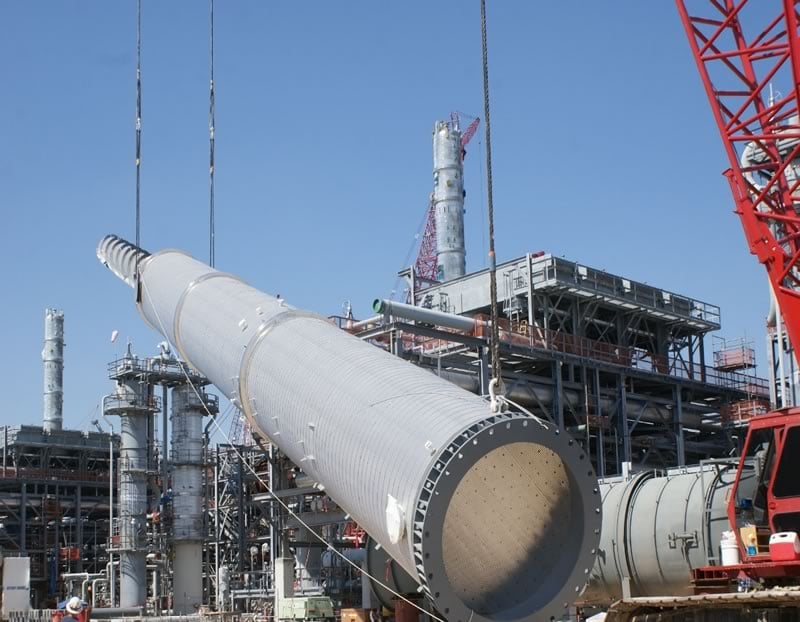
Retrofits
At Zeeco, we understand the vital role thermal oxidizers, also known as incinerators, play in the destruction of hazardous waste gases. It's one reason we maintain a wide inventory of parts and critical components for ready for immediate shipping. Need on-site repair? Our global Rapid Response Team is as experienced and knowledgeable as they come and equally committed to returning your product to service in the shortest amount of time. Zeeco also offers emergency rentals when the unexpected occurs to get your operation back online fast.
- Complete parts inventory for every thermal oxidizer / incinerator system with overnight delivery available
- Rapid Response Team for emergency diagnostic service and repairs
- Global technical services, including preventive maintenance, installation and commissioning
- Emergency rentals
- Thermal oxidizer/incinerator system training
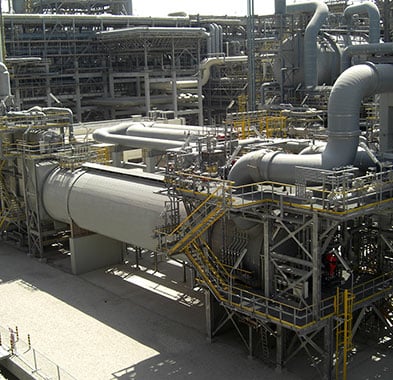
Services we offer
MARKETS WE SERVE
Zeeco can provide combustion and emissions control solutions wherever hydrocarbon processing takes place. Customers can find our equipment and services in upstream, midstream, and downstream oil and energy processes.
We also offer products and support for other industries and applications such as tank/terminal loading and storage, pharmaceutical, carbon black, pulp & paper, steel, food processing, and more.