Offshore Products and Services
CATEGORIES:
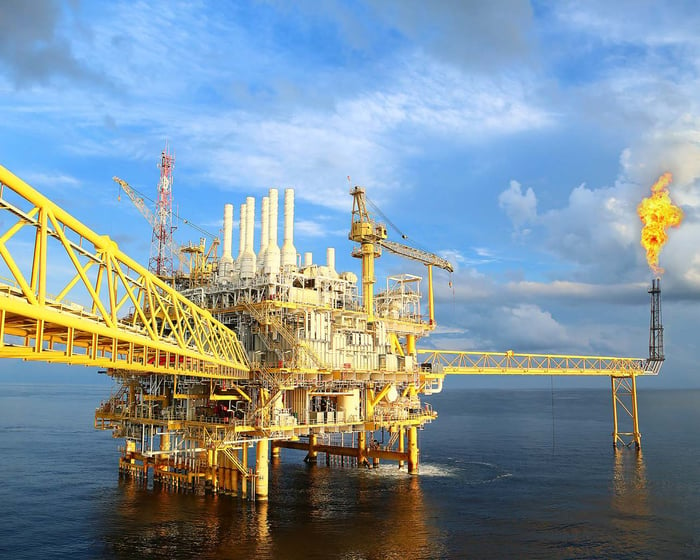
For offshore facilities, a flare is more than a single piece of equipment. Offshore flares are complex systems that require a network of integrated systems to operate. From the flare header to process staging and smokeless combustion, Zeeco has the expertise and technical knowledge to help keep your people safe and minimize the environmental impact of your platform or vessel.
At Zeeco, our decades of combustion experience with the most challenging offshore flaring projects in the world drive us to develop innovative solutions. Because these systems are complex, it is critical to choose a provider with proven expertise in the design, installation, and commissioning of the equipment. Our offshore and Floating Production Storage and Offloading (FPSO) flare systems operate around the world, including in the Gulf of Mexico, South China Sea, South America, India, Africa, and North Sea. Zeeco is proficient at troubleshooting, improving, and replacing the flare equipment of all major manufacturers.
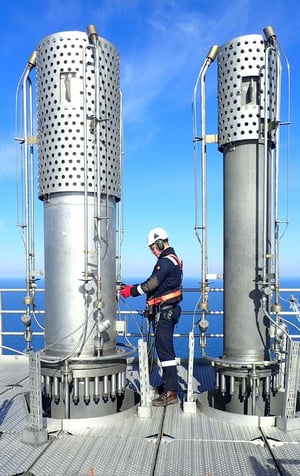
Moving Forward.
Most offshore work involves reinvigorating and extending the life of existing assets. Move now to prepare your flare system for upcoming environmental and operational standards.
High-Integrity VariJet™ (Variable Jet).
Variable exit technologies have been improving high-pressure flaring for decades, but only Zeeco ensures a high-integrity closure of the tip during standby. Fully closing the discharge head vastly improves turndown, mitigates flame impingement, and preserves the integrity of all flaring equipment.
Utility Flare High-Pressure Air Assist (UFHPAA).
Developed for retrofitting smokeless capacity to low-pressure (LP) flares with no steam, our UFHPAA utility flare technology brings significant smokeless capacity with compressed air through small bore piping. Typical retrofits require no structural mitigation to the stack or boom. Perhaps more importantly, the flame shaping of the LP flows prevents flame lick and can further enhance the lifespan of adjacent flaring equipment.
Sonic Flaring.
Zeeco’s high-pressure (HP) flare tips use the energy in the gas stream to improve smokeless performance while achieving a 98.5% or higher destruction efficiency. The ZEECO® UFX™ single-point sonic tip provides a low cost, highly efficient smokeless flaring solution. The UFX is also recommended for operators downsizing systems due to field depletion or to meet zero routine flaring.
The high-pressure Multi-Jet (MJ) flare system delivers superior flame stability and high destruction efficiency for 15 psig (1 barg) or higher applications requiring smokeless flaring and low radiation levels. These flares are commonly designed to be combination high- and low-pressure systems, incorporating LP reliefs within the flame envelop of the high pressure gases. This combination design reduces flame impingement between flare tips and requires fewer pilots.
Liquid Flaring.
Zeeco’s liquid flaring systems are designed for both smokeless and non-smokeless combustion of waste fluids. Smokeless flares require specialty systems designed to use an outside source or assist media such as steam, air, gas, or water to achieve smokeless burning. High pressure may also be utilized in the incoming fluid stream to atomize the wastes and promote smokeless combustion.
Flare Gas Recovery.
As a world leader in the design and supply of Flare Gas Recovery (FGR) systems, Zeeco designs systems to work with your existing flare to help achieve zero routine flaring. With the properly engineered and designed system in place, waste gases are recovered, processed, compressed, and returned to the plant to be reused as fuel rather than flared. This reduces both fuel and flare maintenance costs. Zeeco’s FGR systems will pay you back through fuel savings and help your plant meet current and future regulations by dramatically reducing CO2 platform emissions.
Ballistic Ignition.
The ZEECO® ZIP™ (Zirconium Instant Pressurized) ignition system was developed for, and is used extensively, in the North Sea. The system eliminates continuous pilot gas usage and achieves more reliable ignition than direct electrical spark technologies. When used in tandem with FGR and a liquid seal, zero hydrocarbon emissions can be achieved during continuous operation – compliant with ‘Zero Routine Flaring by 2030’ initiatives. All ignition components are entirely removed from the heat-affected zone to deliver years of reliable operation.
Zeeco is the only company in the world to offer a highpressure ballistic ignition system. While low-pressure systems use pellets requiring an armed detonation to initiate the sparks upon exiting the system, Zeeco’s high-pressure system uses zirconium-filled pellets without internal explosive material. To ensure safe operation, our zirconium pellets require a high-velocity impact with a striker plate to shower the flare tip exit with sparks and ignite the flare gas.
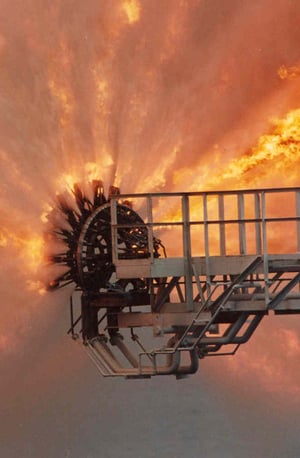
API Compliant Pilot.
Given the criticality of flare pilots, industry leaders and international experts came together to set API criteria for evaluating acceptable flare pilot performance during various operating conditions. Using an APIrecommended pilot test stand at Zeeco’s combustion research and test facility – the largest of its kind in the world – the HSLF™ flare pilot has been proven to stay lit under hurricane-force wind (274 km/h, 170 mph) and rain (131 cm/h, 51 in/h). Not only has the HSLF pilot been proven through testing, but our customers have reported it was the only flare pilot to operate continuously when their facilities were directly hit by hurricanes Ike and Rita. Zeeco’s HSLF flare pilot employs sophisticated castings in lieu of high-stress welding and machining to maximize the pilot’s operating life. Additionally, the HSLF is one of many ZEECO pilots that can be retrofitted to competitor flare systems.
Emission Monitoring.
Zeeco’s combustion electronics take the guesswork out of the combustion process. The FlareGuardian™ direct flare monitoring system measures combustion efficiency (CE) in real time, allowing operators to achieve - and verify - true CE (often 99.5% or higher) well above typically assumed rates (98%). Zeeco’s Contour™ delivers automated, real-time, direct monitoring, as well as smokeless injection media control at a fraction of the cost of indirect measurement systems.
Download Brochure