Sulfur Recovery Unit: Thermal Oxidizer
CATEGORIES:
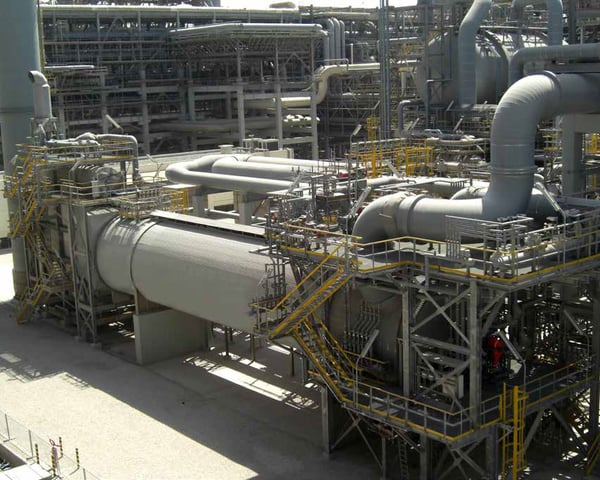
Thermally treating waste matter is a primary method for disposing hazardous and non-hazardous materials worldwide—it’s safe and effective. Zeeco offers a complete line of vapor and liquid incinerators (also known as thermal oxidizers) to dispose of waste streams such as tail gas, acid gas, chlorinated hydrocarbons, and other waste gases and liquids. In addition, multiple waste heat recovery options can make thermal oxidation an economical and energy efficient waste disposal process.
Custom Engineering and Reliability
Zeeco is a world leader in the development of combustion solutions for the refining, petrochemical, pharmaceutical, and power generation industries. Our staff members have extensive experience in design, fabrication, and operation of sulfur-bearing waste thermal oxidation systems. Zeeco also has a proven track record of producing the world’s largest and most advanced thermal oxidizers for disposal of sulfur-bearing compounds. Our thermal oxidation systems are custom- engineered to meet our clients’ specific needs.
Equipment reliability is essential for profitable plant operations. For this reason, Zeeco chooses quality components and materials for all of our products to maximize service life and eliminate unnecessary downtime.
High Destructive Efficiencies
Zeeco achieves high destruction efficiencies (DRE) during the waste incineration process by optimizing the following parameters for each specific process scenario:
1. TIME: maintaining a minimum residence time between 0.7–2.0 seconds.
2. TEMPERATURE: designing the equipment to operate at a temperature that is significantly higher than the autoignition temperature of the sulfur compounds in the waste stream (~700°F or 370°C). Zeeco’s sulfur-bearing thermal oxidation systems typically operate at temperatures between 1200-1650°F (649-900°C).
3. TURBULENCE: ensuring that waste gas is introduced in a manner that results in a homogenous fully reacted effluent.
Due to the relatively low operating temperature, NOX formation during this process is limited. Operating temperatures greater than 1450°F (788°C) are often recommended in processes where carbon monoxide emissions are likely to become important. Due to the large amount of heat generated by the thermal oxidizer, many Zeeco systems incorporate waste heat recovery equipment to further reduce operating costs by generating steam and/or hot oil required for other plant operations. The hot flue gases can also be used to preheat combustion air and/or waste gas to reduce fuel consumption.
A resulting byproduct of the sulfur oxidation process is sulfur dioxide (SO2), which exits in equilibrium with a small amount of sulfur trioxide (SO3). The sulfur trioxide can form sulfuric acid (H2SO4) at low temperatures, which can be a significant issue if it is allowed to condense on and corrode the thermal oxidizer’s outer carbon steel shell. Zeeco minimizes acid corrosion by maintaining the shell temperature above the sulfur dew point temperature.
Many chemical processes produce SO2/SO3 (SOX) levels that are small enough that further flue gas treatment is not necessary. However, if SOX emissions are greater than local environmental requirements allow, Zeeco can also supply caustic scrubbers to reduce the SOX emissions to acceptable levels.
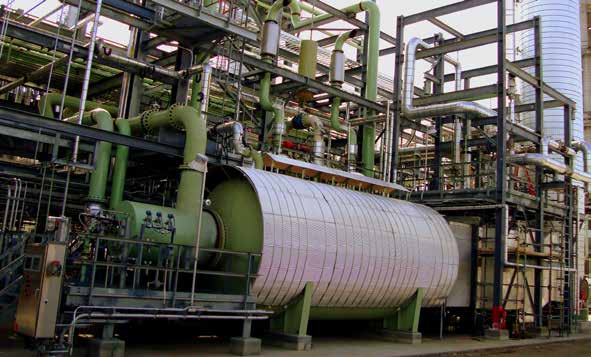
Sulfur Recovery Process
Sulfur-bearing waste thermal oxidation systems typically treat the “tail gases” produced during the sulfur recovery process in a petroleum refinery or other hydrocarbon processing plants. The sulfur recovery process recovers elemental sulfur from the refining processes and the tail gas thermal oxidizer serves to thermally treat the residual hazardous sulfur emissions to limits permitted by national and local air quality requirements.
Proven Performance
Zeeco has provided combustion and environmental solutions around the world for more than 35 years. Let us put our experience to work for you. Contact us today for more information on Zeeco’s full line of thermal oxidation products, services, and replacement parts.
Typical Sulfur Recovery Process
In addition to sulfur tail gas thermal oxidizers, Zeeco also supplies other equipment used in the sulfur recovery process, including reaction furnaces, inline heaters, reducing gas generators, high intensity burners, and waste heat boilers.
Download Brochure