ProFlame™ and Entergy
CATEGORIES:
Cleaner power to the people
Situation
Entergy Corporation owns and operates power plants across the Gulf States and Arkansas, generating 30,000 megawatts of electricity to its more than 2.8 million utility customers. The company has advanced its clean generation strategy in part by boosting the energy supplied with clean, efficient, natural gas-fired combined cycle units. In 2012, Entergy looked to replace the capacity of retired Units 1 and 2 and operational Unit 3 at its Ninemile 6 facility in Westwego, Louisiana, with a state-of-the-art combined cycle gas turbine (CCGT).
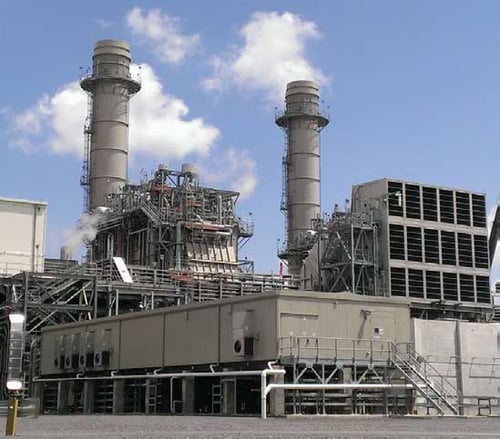
Challenge
Entergy teamed up with CCGT industry leaders General Electric, Vogt Power and Zeeco to engineer the key components for the plant. These included the gas turbines to provide direct electrical power; heat recovery steam generators (HRSG), where steam is produced from the turbine exhaust gas then is used to turn the steam turbine, adding more electricity to the grid; and finally, Zeeco’s duct burners which provide supplemental heat to the HRSG and minimize emissions from the turbine exhaust gas.
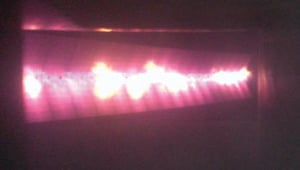
Construction of the plant was completed in late 2014; however, during commissioning, concerns were raised over the reliability of the duct burners when they would mysteriously shut off during low-load firing conditions. What lay behind the shut offs? Was it the turbine exhaust gas flow distribution across the duct burner? Fuel delivery to the duct burner? Flame stability of the duct burner? The shut-offs occurred just below 30% of the maximum rated capacity, where the low-load firing was supposed to operate at 25%.
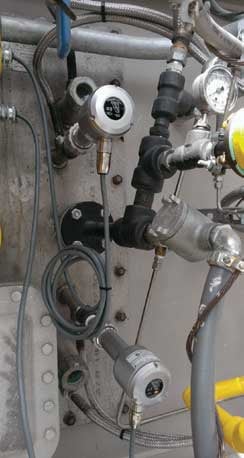
Solution
Zeeco’s engineers went straight to work deconstructing the problem facing Entergy’s Ninemile 6 plant and the unusual shut-off of Zeeco’s duct burners during low-load firing conditions. They quickly determined that Zeeco’s duct burners were performing as designed, but the existing flame scanners caused the duct burners to trip prematurely at low-load firing conditions, even after properly tuning them for worst case conditions. Zeeco replaced the existing flame scanners with its own ProFlame™ integrated flame scanners, which provide proven, reliable flame detection across the turndown of the duct burner. The difference between ProFlame and other competitor flame scanners lies in the ProFlame state-of-the-art signal processing and the ease in which to tune the scanner. The ProFlame display provides instant feedback on whether the scanner settings are correct or need adjustment. Zeeco’s ProFlame scanners provided reliable flame detection for a low-low firing condition at 18% maximum rated capacity. Almost immediately, Zeeco engineers discovered that the ProFlame scanners not only detected the flames over turndown, but also safely discriminated the target burner element’s flame from adjacent burner element flames within the duct burner array.
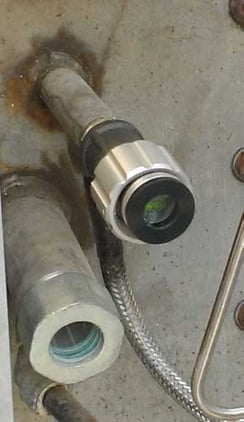