A Cost-Effective Solution to Emission Compliance
CATEGORIES:
High capital costs are a significant challenge for storage operators in ensuring their older vapour recovery units are emission compliant. A vapour recovery unit revamp is a cost-effective solution in ensuring the unit is compliant with the latest regulations.
Throughout the world, vapour recovery systems are a common sight at refineries, distribution terminals, and tank storage facilities, handling the transfer of products ranging from gasoline to aromatics such as benzene and xylenes, and increasingly, crude oil.
When hydrocarbons are transferred between ships, rail, road tankers, and storage tanks, a fraction of the product is typically released as a vapour. While the fraction may be small, the cumulative release can be substantial because of the large quantities of product – typically 10,000 m3 /hr to 1000 m3 /hr – and higher vapour flows typical in marine loading applications. Unless vapour control technology is used, vapour is released to the atmosphere having a detrimental effect on the environment, health, and neighbouring infrastructure.
Activated carbon vapour recovery (Figure 1) remains the preferred technology in most applications, often referred to as the best available technology (BAT). These systems provide operators with maximum flexibility, handling an extensive range of products and featuring a wide turn down ratio from 0% to 100% of the design flow and inlet concentrations.
Figure 1. A typical wet VRU featuring two carbon beds, two liquid ring vacuum pumps, a glycol separator vessel, and an absorber column.
Legislators worldwide are continually demanding more emission control capability from operators and system designers. Current requirements are now set as low as 50mg (HC) / Nm3 for any one hour’s average emission in parts of Europe. Naturally, system providers must adapt and develop designs to meet these new regulations and demands. Environmental pollution legislation will always remain the driver for development of vapour recovery technology and operator capital investment, because of the large financial penalties for a violation of emission requirements. But in situations where a large capital investment is not affordable – what options do operators have when facing new regulation or increased terminal throughputs?
It is imperative that vapour recovery units are sized correctly for the vapour flow, vapour concentration, and desired emission targets. Older units may not be able to keep up in the face of increased throughputs or new regulations. A new vapour recovery unit designed specifically for a lower emission output and increased capacity is one solution; however, these have high capital costs and long lead times. Alternatively, it is often possible to revamp, renew, and upgrade existing vapour recovery units on site – minimising capital cost, lead times, and plant downtime.
Vapour recovery units can be overhauled and upgraded in various ways, depending on the requirement of the end user. Fundamentally, a greater mass of activated carbon and an increased vacuum flow rate is required. Adding extra activated carbon is not always feasible, however. Typically, the activated carbon vessels do not have free volume available. In scenarios where it is not possible to replace the carbon bed vessels with larger units, the time in which each vessel is in the adsorption phase can be adjusted, within design limits, to ensure emission limits are not exceeded near the end of each cycle.
It is becoming advantageous in many scenarios to replace ‘wet’ liquid ring vacuum pumps (LRVP) and seal fluid systems with a ‘dry’ retrofit. This replaces the LRVP (modelled in Figure 3) with typically a dry screw or rotary vane pump matched specifically to physical conditions present within process and on site. Once seen as a robust form of vacuum supply – ‘wet’ systems typically require more onerous maintenance as the seal fluid must be kept in a constant composition for it to perform correctly. Now, due to advancements in design and capability, dry system vacuum pumps are becoming more versatile with the ability to perform reliably in extreme conditions and varying temperatures because of gasoline injection or heat tracing for temperature management. An ideal time to integrate these additional systems is during a VRU revamp. Another motive for operators to remove LRVP’s and replacing with screw pumps is with the increasing use of ethanol blended gasolines. The LRVP seal fluid becomes contaminated with ethanol during use – and will quickly dilute to a level, reducing the effective capacity of the pumps. A dry screw pump does not suffer from these issues.
Figure 3. LRVP.
Where the capacity of the VRU has been increased, it is also generally required to increase the vacuum pump capacity, as the adsorbed hydrocarbons now must be regenerated in a shorter time period. For a low emission vapour recovery unit, the vacuum pump must be capable of achieving relatively low vacuums; 50 to 35mbara, whilst regenerating the carbon bed in a much shorter period. This can be achieved by replacing the existing vacuum pump system with a larger capacity system. The negative side of the reduced adsorption time is that the working life of the carbon is reduced as a result of more regeneration cycles in a given time.
Increases in vacuum capacity initiate changes in subsequent equipment within the vapour recovery unit downline from the vacuum pump. For example, in vapour recovery units that feature a liquid ring vacuum pump, the glycol separator (Figure 4) would also need to be upgraded with a larger vessel to accommodate the greater flow capacity required by a higher capacity liquid ring vacuum pump, which has been resized to accommodate the increased vapour flow.
Figure 4. A glycol separator.
The absorber tower may also need to be replaced to accommodate higher vacuum pump capacities or changes to the absorbent’s properties: temperature and vapour pressure. Absorption efficiency is directly related to the absorbent’s physical characteristics (temperature and vapour pressure), the absorbent and gas (vapour) flow, and the absorber diameter and height, all of which will need to be reviewed and potentially increased when a larger vacuum pump is installed.
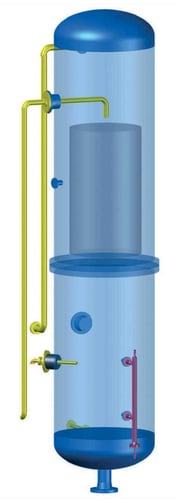
A complete absorber tower replacement is expensive; alternative options may include the addition of a pressure control valve in the recycle line from the absorber column to the carbon beds. This can be sized to maintain an operating pressure within the absorber tower to improve the performance of the process. Consideration should also be given to secondary factors, such as increased temperatures in the vacuum pump discharge, which may subsequently require additional cooling, perhaps in the form of gasoline injection or, in the case of a wet system, an increase in size of the installed heat exchanger.
As well as increased capacity and lower hydrocarbon emissions, vapour recovery unit revamps can also offer greater control, features, versatility, and safety for the end user. This can be achieved by means of adding extra vacuum pumps for redundancy; new CIM/CEM upgrades and analysers for precise emissions monitoring; upgraded valves and actuators; and temperature, pressure, and level transmitters. New equipment can be seamlessly integrated with an upgraded PLC/HMI system coupled with a bespoke control theory to reduce the chances for a high emission incident to occur. An additional benefit of replacing existing equipment is that it removes the legacy problem of equipment that is no longer supported by the OEM, particularly with respect to PLC/HMI systems.
Figure 6. Pipe skid modifications.
Maintenance of the revamped VRU is equally as important as the selection of the right vendor and subsequent engineering carried out during the revamp. Activated carbon in low emission VRUs is subject to greater mechanical force and, in some cases, unwanted chemicals, which prohibit adsorption. Therefore, it is imperative that recommended service intervals are adhered to and the activated carbon tested periodically, thus mitigating the risk of continued damage that would otherwise lead to sudden failure.
A vapour recovery unit revamp is a robust compromise for operators seeking to increase terminal capacity while remaining emission compliant, or for operators seeking new HC emission regulation compliance without the capital outlay of a new VRU. Despite the extensive replacement of equipment required – a vapour recovery revamp is still a more cost effective solution than installing a brand-new unit in many scenarios.
A successful VRU revamp requires significant experience, like that of Zeeco, with a wide variety of VRU systems due to the complex interactions of the equipment across the system. Zeeco can also offer service on equipment that was not originally supplied by them.
For More Information
This article was written by Tom Olver, technical sales, projecting and start-up engineer for Zeeco Europe.
Download Article