Removing Obstacles to Increase Liquid Loading Throughput at Marine Terminal Facilities
CATEGORIES:
Gayla Broostin and Greg V. Seefeldt, Zeeco Inc., USA, outline the obstacles that need to be removed to increase liquid loading throughput at marine terminal facilities.
The anticipated demand for marine loading will require that marine vapour control system (MVCS) capacity be increased beyond what may be currently available at many facilities. Upgrades, optimisation or expansion of existing systems or installation of portable MVCSs to meet temporary demand spikes may be needed.
How much liquid loading throughput a marine terminal facility can deliver is a function not just of the ability to pump liquid from tanks to vessels, but also the capacity and reliability of the vapour control system. MVCS design and operation can be complex due to the stringent emission and safety requirements that must be met. Changes to these requirements, as well as increased demand for marine transportation of crude oil and other cargoes, has added complexity to system design and operation (Figure 1). In today’s operating environment, older or even decommissioned terminals are being pressed into service. Many owners and operators are struggling to meet varying and sometimes even conflicting demands. So, what are best-in-class strategies to improve reliability, meet current emission regulations, and increase the capacity of MVCSs through retrofits, upgrades, rental equipment, and servicing?
System Purpose and Regulatory Requirements
Figure 1. Typical marine vapour combustion system in operation on the US Gulf Coast.
Vapour control for marine and other types of liquid hydrocarbon loading came about due to environmental concerns. In the US, the Environmental Protection Agency (EPA) and state air quality boards dictate the exact emission requirements that must be met, and the US Coast Guard (USCG) regulates the safety aspects of marine vapour control. Both emission and safety requirements have become more restrictive over the past several years, such as those of the USCG, which underwent a significant revision in 2013. New emissions requirements include increased volatile organic compound (VOC) destruction efficiency and reduction of combustion unit nitrogen oxide (NOX) levels. When seeking to recommission older facilities or upgrade the capacity of existing facilities, the newer regulations are likely to impact a variety of equipment decisions.
Strategies for Improving Existing System Performance
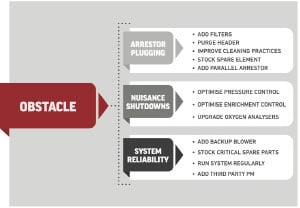
Key components of all MVCSs include detonation arrestors, oxygen analysers, blowers, and recovery and combustion units. Since marine vapour control was first widely implemented in the 1980s, much has been learned about the best practices for maintaining and operating these components, as well as control and operational improvements that can be made to increase system reliability and capacity (Figure 2).
The primary safety device in all vapour control systems is the detonation arrestor. Unfortunately, it is also the primary maintenance issue in most systems. The many small passages in the arrestor element tend to collect particulate matter that restricts vapour flow. This particulate is most often rust from the vessel or facility vapour piping but can also be compounds that have precipitated out of the vapour stream. Due to the stringent design requirements for these units, the housings are very large, and the removal and cleaning of the internals can be difficult and time-consuming. There are several strategies for limiting downtime and capacity restrictions that are due to arrestor plugging. Regularly scheduled cleaning and inspection by experienced vapour control technicians will help determine the best course of action.
Over time, particulate that cannot be removed by routine cleaning may accumulate deep inside the arrestor element, resulting in increased pressure drop and restricted capacity. Deeper cleaning methods or replacement of the arrestor element is then required.
Other strategies for reducing downtime due to arrestor plugging include:
- Installation of pre-filters upstream of system dock safety equipment to capture rust coming from the vessel being loaded.
- Installation of two detonation arrestors in parallel to provide additional flow area or online switching between units when one becomes plugged.
- Onsite stocking of spare elements and/or complete arrestors.
Purging the vapour header with natural gas, propane or nitrogen after each loading operation may also prevent plugging of system components such as burners and detonation arrestors. Purging removes moisture and prevents heavy hydrocarbons contained in the vapour from being left to condense inside the vapour header between loading operations.
While oxygen analysers do not affect the capacity of the system, they are required for its operation and their malfunction can result in costly downtime. Marine vapour control applications can successfully utilise several analyser technologies, some of which have been in use for many years and others which have only recently come about. Proper analyser selection should consider both the operating conditions and the maintenance capabilities of the facility. Analyser systems are complex and should be maintained and adjusted only by highly qualified personnel. Facilities without dedicated analyser technicians should consider analyser types that require minimal adjustment or consider having the analysers regularly maintained by an expert technician. Reliability of existing oxygen analyser systems may be improved by purging the analysers and their associated sample system with nitrogen after each use in order to remove moisture and contaminants.
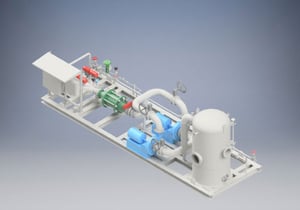
and backup blowers.
A blower is utilised in most vapour control systems to move the vapours from the dock and through the end control device. The blower’s capacity and reliability are critical to system operation. For this reason, it is recommended that multiple vapour blowers be installed. Additional blowers will allow the system to operate at full or partial capacity should a failure occur. Adding a backup blower is recommended for single-blower systems. Also, if the system capacity is restricted due to high pressure drop, a blower replacement or addition should be considered (Figure 3).
Inadequate pressure control is a common problem in vapour control systems, and it results in inefficient operation and nuisance shutdowns. Pressure control is typically an automated function performed by one or more control loops. Proper set-up and tuning of these pressure control loops is critical. Older systems may also have pressure control issues due to the age and condition of components and may be in need of control system or hardware upgrades. If pressure alarms and shutdowns are an issue, consult an experienced vapour control specialist to evaluate the system and make recommendations for improved pressure control.
Enrichment gas injection is used in most vapour combustion systems. As with pressure control, proper set-up and tuning of enrichment control is critical to proper system operation. The proper tuning and set-up of enrichment control must consider the enrichment process, how it evolves over the course of an operation, and how it affects downstream equipment. An improper enrichment control set-up can lead to nuisance shutdowns, loss of capacity, unnecessary enrichment gas consumption, and overfiring of the combustion unit, resulting in high emissions.
Pilots on vapour combustion units are a common point of failure during system start-up. This is often due to plugging of the fuel flow orifice or shorting of the spark ignition system due to moisture in the ignitor rod. Routine inspection and cleaning of the pilots can reduce these start-up issues. Also, stocking a spare pilot which can be swapped for one that is malfunctioning can save valuable time at start-up.
Because vapour control systems are operated only during loading operations, they may sit unused for long periods of time. An extended period of disuse can quickly result in deterioration of system components. It is highly recommended that a vapour control system be started up and briefly run at least once a month. This will allow any issues to be discovered and addressed prior to beginning a loading operation.
Many system owners utilise the services of third parties specialising in vapour control for annual or quarterly preventative maintenance of their systems. A specialist in vapour control maintenance can efficiently identify potential issues and address them before system downtime results.
Recommissioning Idled Systems
If a vapour control system is to be recommissioned after sitting idle, the scope of work may go beyond refurbishment of existing components to return them to working condition. Changes required for compliance with current regulations may also be needed. The addition of temperature control to combustion units, upgrading of valves to fire-safe types, and adjustment or replacement of pressure relief valves are some of the changes that are commonly needed to bring older systems into compliance. Determining a scope of work for bringing an idled system back online should be supported by personnel familiar with the applicable safety and emission requirements.
Increasing Vapour Handling Capacity
The vapour handling capacity of a system depends both on the sizing of the piping system and the capacity of the end control device to recover or destroy the hydrocarbons present in the vapour stream. Both factors must be evaluated as part of an effort to increase overall system capacity (Figure 4).
Figure 4. Existing vapour combustion unit undergoing retrofit for improved capacity and performance.
If the design vapour handling capacity of an existing system cannot be reached in actual operation, then an evaluation of the complete system should be performed. Such an evaluation can determine whether piping or component changes would allow an increase in vapour flow rates. These changes might include replacement of detonation arrestors with larger or lower pressure drop units or increasing vapour piping line sizes.
If pressure drop cannot be decreased by piping or component changes, the installation of additional blower horsepower should be considered. If the changes to the piping system or blower horsepower result in higher vapour flow rates than the end control device was designed for, then it must be evaluated to determine what effect the change would have on its operation. Low emission vapour control systems may be more sensitive to changes in vapour flow, and both their capacity and ability to maintain required emission levels must be considered.
If a temporary increase in vapour handling capacity is needed or a permanent installation is unavailable, vapour control equipment is available for short or long-term rental. A rental system could be a complete system with both dock safety and vapour combustion equipment or could be a partial system that could be coupled with permanent equipment onsite (Figure 5).
Figure 5. Zeeco portable vapour combustion unit in use during maintenance of a vapour recovery unit.
Early planning for the implementation of rental equipment is recommended. This may include adding a pipe tee into the existing vapour header to simplify connection of the rental equipment or having the site certified for the use of rental equipment. In the US, for instance, a facility must be certified for use of rental or portable marine vapour control equipment by an authorised certifying entity.
Other Considerations
In addition to the equipment-related strategies detailed in this article, proper training of personnel who operate and maintain vapour control systems is of great importance. Operators should be familiar with applicable emissions and safety regulatory requirements as well as operational requirements. Operators who understand the cause and effect of vapour control system adjustments can effectively optimise system operation and increase system uptime by preventing nuisance shutdowns. Many vapour control system manufacturers and consultants can provide training on the operational and regulatory aspects of vapour control systems.
In the US, certification of MVCSs by an authorised third-party, referred to as a certifying entity (CE), is required. Developing a relationship and open dialogue with an experienced CE or working with a vapour control company who understands and facilitates the certification process will prevent delays due to certification issues.
Conclusion
Marine vapour control has several unique challenges that must be effectively managed in order to optimise performance, operate safely, and remain in compliance with ever-changing regulations.
The goals of vapour control are to safely and efficiently collect vapours generated in loading applications and to minimise pollutants that are vented to the atmosphere. Implementation of the strategies in this article will assist owners and operators who seek to improve their current operation, recommission a previously idled operation, or add new capacity to an existing operation.
Download Article