Taking on the Tiling Puzzle
CATEGORIES:
David A. Short, Zeeco, UK, describes how an upgrade to the design of the traditional radiant wall burner tile used in process burners was achieved.
Radiant wall burner tiles play an intrinsic part in maintaining furnace temperature and operating stability and efficiency. Historically, radiant wall burner tiles were manufactured in four pieces using kiln-fired, hand-moulded firebrick clays, supported by external side fixing cleats. During the 1970s, the majority of radiant wall burner tiles were produced in two pieces using conventional alumina silica castable material. A retention system of side and bottom cleat fixings was welded to the front burner mounting plate (Figure 1). This design was adopted by major process burner manufacturers and in most cases still applies today.
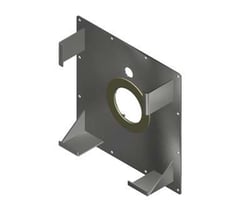
side and bottom cleat fixings.
However, this design is not without challenges. The primary issues are the weight of the tile and the failures of the retention system. Even when cast in two sections, the dense refractory material is heavy and cumbersome to install, and it requires an extensive anchor and support system, as seen in Figure 1. The traditional retention system often allows hot gas to penetrate around the burner tile expansion gap and due to adjacent refractory shrinkage or refractory movement, the recirculating/escaping gas not only reduces the furnace efficiency and stability, it increases the likelihood of premature failure of the cleats through potential overheating of the burner mounting plate or furnace casing.
To ensure a tile performs as expected, end-users must consider critical selection criteria for refractory material. These include:
- Furnace operating temperature
- Furnace cold face temperature
- Gas or oil firing
- Oxidising or reducing atmosphere and gas composition
- Roof, wall or floor mounted burners
- Likelihood of gas erosion and/or chemical attack
- Likelihood of direct flame impingement
- Thermal cycling conditions.
A New Modular Tile Design
Engineers at Zeeco set out to create a tile with greater integrity and reliability. The resulting design, named Zeecolite, is a one piece composite radiant wall burner tile (Figures 2 and 3). Key components of this design include an erosion-resistant hot face and thermally efficient, lightweight material backup insulation with secure Inconel stainless steel embedded anchorage.
Figure 2. Zeecolite one piece composite radiant wall burner tile – hot face.
Figure 3. Zeecolite one piece composite radiant wall burner tile – cold face.
The one piece modular design uses a specially-formulated 62% alumina low ferric oxide 1700˚C low cement castable as the hot face, backed up with ceramic fibre insulation boards (Figure 4). The design provides both thermal efficiency and erosion resistance – fundamental criteria for burner performance and firebox reliability.
Figure 4. Side view of modular tile design showing ceramic fibre insulation boards and embedded anchor system.
The tile assembly is self-supporting with a four-point Inconel stainless steel embedded anchoring system. The embedded, fully-enclosed system is used to attach the tile module to either the furnace casing or the burner mounting plate. The anchor system is completely independent of the surrounding furnace refractory and the combustion components of the burner system. Embedding the anchors in the cast section prevents the problems associated with metal fatigue and oxidisation (Figure 5).
Figure 5. Side view of modular tile design showing attached eye bolts for manoeuvring tile into place.
Behind the hot face, the ceramic fibre insulation board provides the thermal efficiency and reduces weight. The resultant tile module with anchor system provides improved thermal efficiency and lower weight, fundamental needs in today’s modern furnaces.
Addressing Longevity and Start-Up Issues
Zeecolite tile is pre-dried to 360˚C to ensure the removal of both free and chemical water. This process negates the common problem of thermal cracking or tile failure during start-up procedures. The fully protected anchor system ensures the long-term integrity of the support system and prevents any forward movement of the tile in relation to the burner gas tip, both longevity and reliability challenges common to traditional tile designs. The addition of the low mass ceramic fibre insulation improves thermal efficiency, which also reduces energy-related costs for keeping the furnace operating within design specifications and efficiency targets.
Applications
The one piece modular tile has been designed for use in flat flame side-fired burner applications in primary reforming furnaces. Both the hot face cast section and the thickness of the ceramic fibre insulation board can be varied based on the particular parameter of the furnace or application; this design is suitable for any existing or new construction regardless of wall thickness or the composition of the surrounding refractory.
Installation
The burner tile module is designed to be easy to install for both new and retrofit applications. The embedded stainless steel anchors protrude through the rear ceramic fibre insulation boards for bolting to the exterior mounting plate. To first hoist the modules up to the mounting location on the furnace wall, eye-bolts that thread onto the anchor bolts are typically supplied with the tile assemblies. Once in place, the mounting system ensures the anchors are able to suspend the burner tile module without any movement due to gravitational torque – meaning the tile module will not impart any significant loads or stresses to the surrounding lining system. This is a particular advantage where delicate materials are used for the lining system, such as refractory ceramic fibre (RCF) modules. Fitting the tile module into position can be carried out internally or externally, depending on whether the module is in turn fixed to a burner mount plate or directly to the furnace casing.
If the anchor bolt pattern does not match the existing arrangement on the furnace mounting plate, additional holes can be drilled in the mounting plate using a template board to locate the holes or, alternatively, the module can be pre-assembled to a new burner mount plate. This type of tile module is in use in many steam reforming furnaces and has delivered thermal efficiency and longevity advantages.
Case Study: Germany
A furnace with side-fired natural draft burners had a refractory wall thickness of 325 mm through the burner tile.
The original tile had a 250 mm thick hot face and used a 1650˚C alumina silicate castable, with two layers of ceramic fibre and calcium silicate boards adding another 75 mm in thickness. The hot face temperature could reach 1200˚C, though for tile design comparison purposes the firebox mid-range temperature used was 1100˚C. The cold face temperature, at ambient conditions of 21˚C and no wind, was 96˚C with a heat loss of 936 W/m2 .
The new tile’s hot face material comprised of 62% alumina 1700˚C low cement castable and was 60 mm thick between anchor webs and 160 mm thick through anchor webs, backed with 165 mm of ceramic fibre insulation boards. The overall module thickness was 325 mm.
The cold face temperature average of the castable sections, with the same ambient conditions, was 60˚C with a heat loss average of 410 W/m2 .
As a result of the application of the new tile, there was a 56% improvement in thermal efficiency with a module weight reduction of 79 kg/tile.
Case Study: Austria
A furnace with side-fired natural draft burners had a refractory wall thickness of 293 mm through the burner tile. The hot face temperature could reach up to 1200˚C, but for tile design comparison purposes the firebox mid-range temperature used was 1100˚C.
The original tile had a 158 mm hot face and used a 1650˚C alumina silicate castable, backed by three layers of ceramic fibre and calcium silicate boards, thus totalling 135 mm. The cold face temperature, with ambient conditions of 21˚C and no wind, was 77˚C with a heat loss of 645 W/m2 .
The new tile’s hot face material comprised of 62% alumina 1700˚C low cement castable and was 58 mm thick between anchor webs and 158 mm thick through anchor webs, backed with 135 mm of ceramic fibre insulation boards. The cold face temperature average of the two castable sections, at the same ambient conditions, was 65˚C with a heat loss average of 468 W/m2 .
Consequently, a 28% improvement in thermal efficiency was achieved with a module weight reduction of 38 kg/tile.
Conclusion
The new tile design has reduced furnace downtime and improved product longevity. In addition, when coupled with improved thermal efficiency, its application has resulted in notable savings on operational and maintenance budgets.
Figure 6. Operating radiant wall burners in furnace using Zeecolite tile.
Download Article