Ejector Technology for Efficient and Cost Effective Flare Gas Recovery
CATEGORIES:
Flare systems are a common sight in the GCC region at oil and gas production, processing, and refining facilities. They offer a safe and reliable method for burning gases during emergency release cases. While flares will always be needed for these emergency cases, the last decade has seen a stronger push to reduce flaring rates during normal, non-emergency conditions by adding Flare Gas Recovery (FGR) systems.
The main goals are to increase efficiency of the facility and reduce air emissions. This paper discusses using ejectors for FGR systems. While ejector technology has been utilized for many years in other services, the concept of utilizing it for FGR is relatively new. A variety of compressor technologies have been utilized for FGR systems including Liquid Ring, Screw, Reciprocating, and Sliding Vane. Each type offers its own advantages and disadvantages; however, some common disadvantages shared by all of these compressor technologies include high operating costs, specialized maintenance requirements, and costly spare parts. Ejector systems are now being considered for many FGR applications as they offer distinct advantages in some applications, especially in smaller Gas-Oil Separation Plants in the GCC region. To compress flare gases to a higher pressure, ejectors utilize a high-pressure medium, commonly water, steam, or fuel gas. In some facilities, this high-pressure medium is already available with existing fuel gas supply or water pumps. This paper will explore the benefits of ejector technology for FGR in detail, including case studies of existing equipment.
BACKGROUND
In recent years, some refinery owners and operators have recovered the gas in their flare networks in lieu of flaring. FGR offers real and tangible benefits:
- Recovered flare gas can be re-used in process heater burners and boiler burners
- Reduced amount of natural gas purchased by the facility
- Extended life of flare system
- Lower greenhouse emissions from facility
FGR also provides some intangible benefits. Reducing the amount of flaring overall reduces the visibility of the flare, improving public perceptions of the facility. This typically results in fewer complaint calls to the refinery from surrounding communities due to flaring.
EJECTORS
In recent years, there has been a larger push to utilize ejectors to recover flare gas. Ejectors are often called Eductors, Jet Compressors or Jet Pumps. In certain situations, ejectors may offer distinct advantages over traditional compression technologies. They have no moving parts in the compression zone, and can handle a wide range of process conditions. They also may offer significant cost savings.
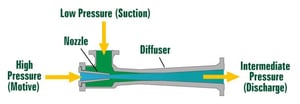
Figure 3 shows the basic operating principle of ejectors. The operation is based on Bernoulli’s principle, which states that as the speed of a flowing fluid is increased, it’s pressure decreases. Conversely, as the velocity of a flowing fluid decreases, its pressure must increase. In an ejector the velocity of the motive (or HP) fluid increases as it passes through the nozzle, creating a low-pressure region within the ejector. This region entrains the low pressure flare gas stream. As the combined HP and LP streams pass through the ejector’s diffuser section, the velocity decreases and the pressure is regained, resulting in an intermediate pressure, which lies somewhere between the LP and HP. The HP stream needs to be at a high enough pressure to ensure the resulting intermediate pressure achieves the required system discharge pressure for the recovered flare gas. If high-pressure water or steam is used, a separator is required downstream of the ejector to separate gas from water. If high-pressure gas is used, there is no need for any downstream separator.
CONCLUSION
Flare systems remain a necessary component for safe operation of many oil and gas production, processing, and refining facilities. However, with tighter emissions requirements, the next decade will see an increase in the number of FGR systems installed to reduce continuous flaring. The sizing, proper selection, and design of FGR systems require a careful and organized approach, utilizing an experienced designer. In many cases, ejectors may be the ideal compression technology for these systems.
Download Technical Paper