Solid Fuel to Natural Gas Conversions for existing Boiler Applications
CATEGORIES:
Zeeco was contacted by a large industrial plant owner to assist them with the fuel changeover of a utility designed solid fuel CFB. Due to current contract requirements and the competitive nature of the industry, the plant owner will remain confidential.
Abstract
Recent discoveries of vast natural gas reserves in the United States have resulted in increased production of Natural Gas, resulting in lower prices. Petrochemical facilities are performing solid fuel conversions on their boilers to natural gas as a cost-effective and efficient fuel solution. Natural Gas is not only economically beneficial but also environmentally efficient with cheaper prices and reduced SO2, NOx, and CO2 emissions. As more facilities consider boiler fuel conversions, it is important to understand all facets of the conversion, from the thermal evaluation of the boiler, to the complete design, supply and installation of the new firing system.
We will provide specific details and recommended practices from a recent Circulating Fluidized Bed (CFB) Boiler fuel conversion application designed for 1.4 billion Btu/hr of heat input for the maximum continuous steam rating. We will also review thermal performance results, design and supply of the complete new gas firing system, and installation conversion assistance for the boiler modifications and firing system installation details.
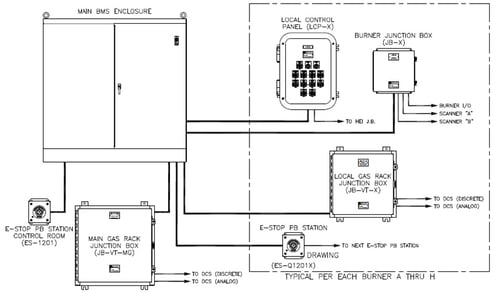
The primary goals of the project are as follows:
- Full Conversion from Petcoke firing to Natural Gas
- Maintain boiler steam design capacity (~1200 kpph)
- Meet permitted NOx requirements – 0.07 lbs/MMBtu
- 25-100% heat input for NOx emissions
- Minimal or no impact on the boiler waterside design
The owner provided the original boiler design information for Zeeco’s review of potential boiler burner retrofitting options. This was the first of two boilers that would require retrofitting Two sister units were built/commissioned on solid fuels approximately three years previously. The units were originally designed with natural gas start-up burners and commissioned for main fuel support via the petcoke. The petcoke was to be fired and combusted via a circulating fluid bed system. Upon initial advisement from the plant owner, they noted that their petcoke fuel contract was no longer cost effective, as this fuel feedstock was significantly higher in price than originally estimated in the plant system’s budget. The boilers were only in operation for less than two years when this decision to switch to natural gas was determined.
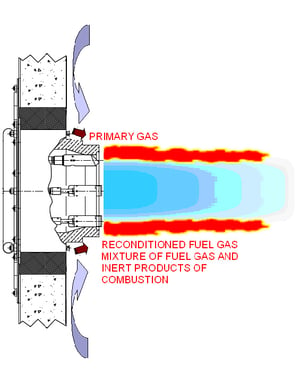
Introduction to Free-Jet Technology
The Zeeco Free-Jet burner series was designed with the specific purpose of maximizing the amount of IFGR to reduce thermal NOx emissions without sacrificing burner performance with respect to flame length, turndown, and stability. The maximization of IFGR means many of the problems associated with using high levels of EFGR to achieve low emissions can be reduced or eliminated. Specifically, Zeeco’s Free-Jet design dramatically reduces or eliminates the need for EFGR by reducing blower power usage, increasing turndown, reducing maintenance and improving flame quality.
Conclusion
Boiler steam load and emissions were met in a very timely fashion, and the plant owner was able to generate plant power within less than a month after the initial boiler start-up. The plant owner operated the boiler and turbine/generator near design capacity for over three months after final commissioning. The effort placed on the entire project, pre and post-award, led to the overall success of the boiler’s conversion. The integration by the plant owner and the three primary engineering parties led to a fully integrated design that was reviewed by all to ensure the timely success of the project. Based upon the success of the first boiler, Zeeco was awarded the contract for the second CFB boiler conversion, and will begin with installation and commissioning to be in mid-2014.
Download Technical Paper