Case Studies
Subscribe to Zeeco Updates
CATEGORIES:
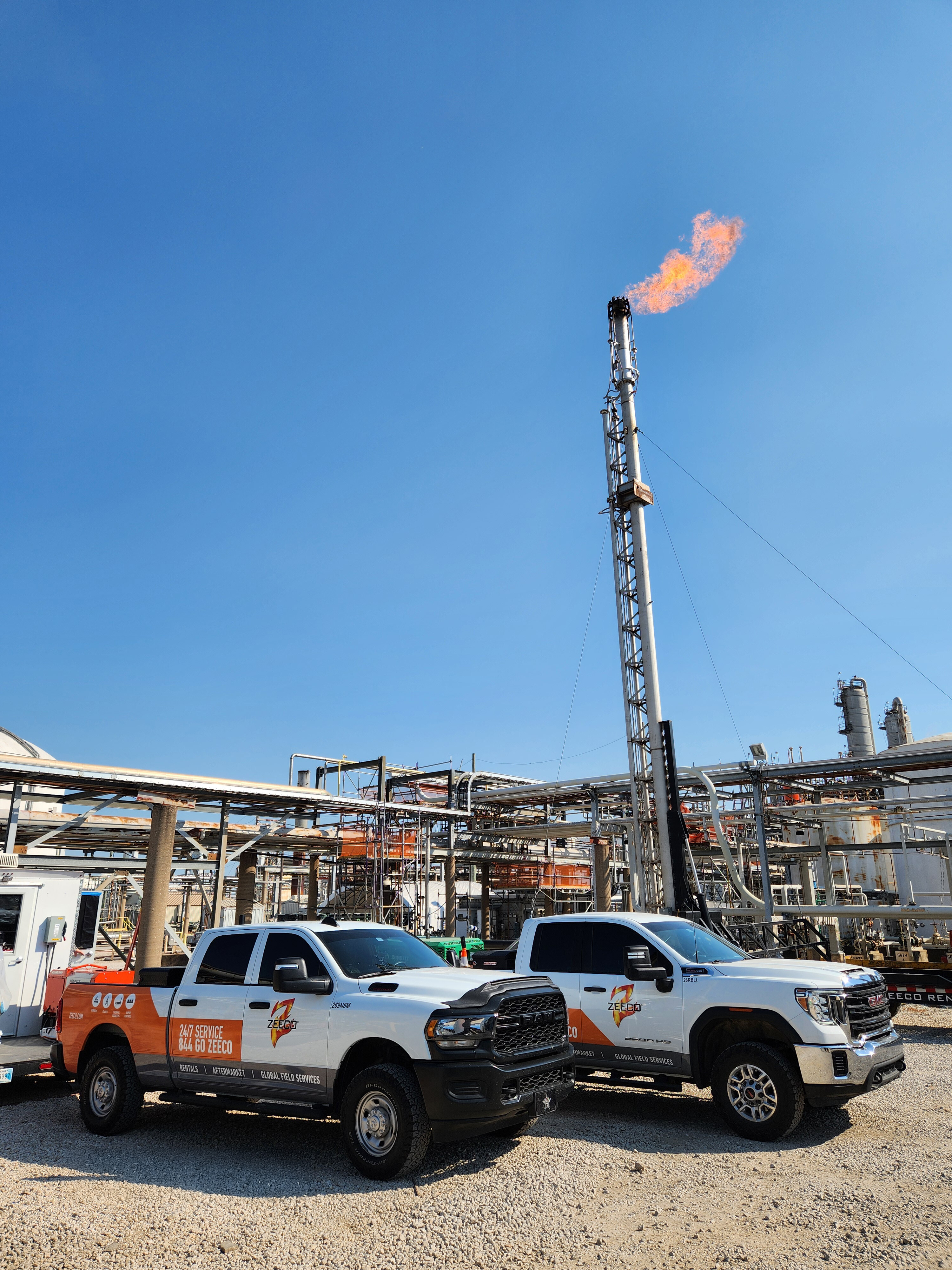
Complete Temporary Flaring & Monitoring Solution
SITUATION In February of 2024, a specialty chemical company in Pasadena, TX, reached out toZeeco..
Read More >>>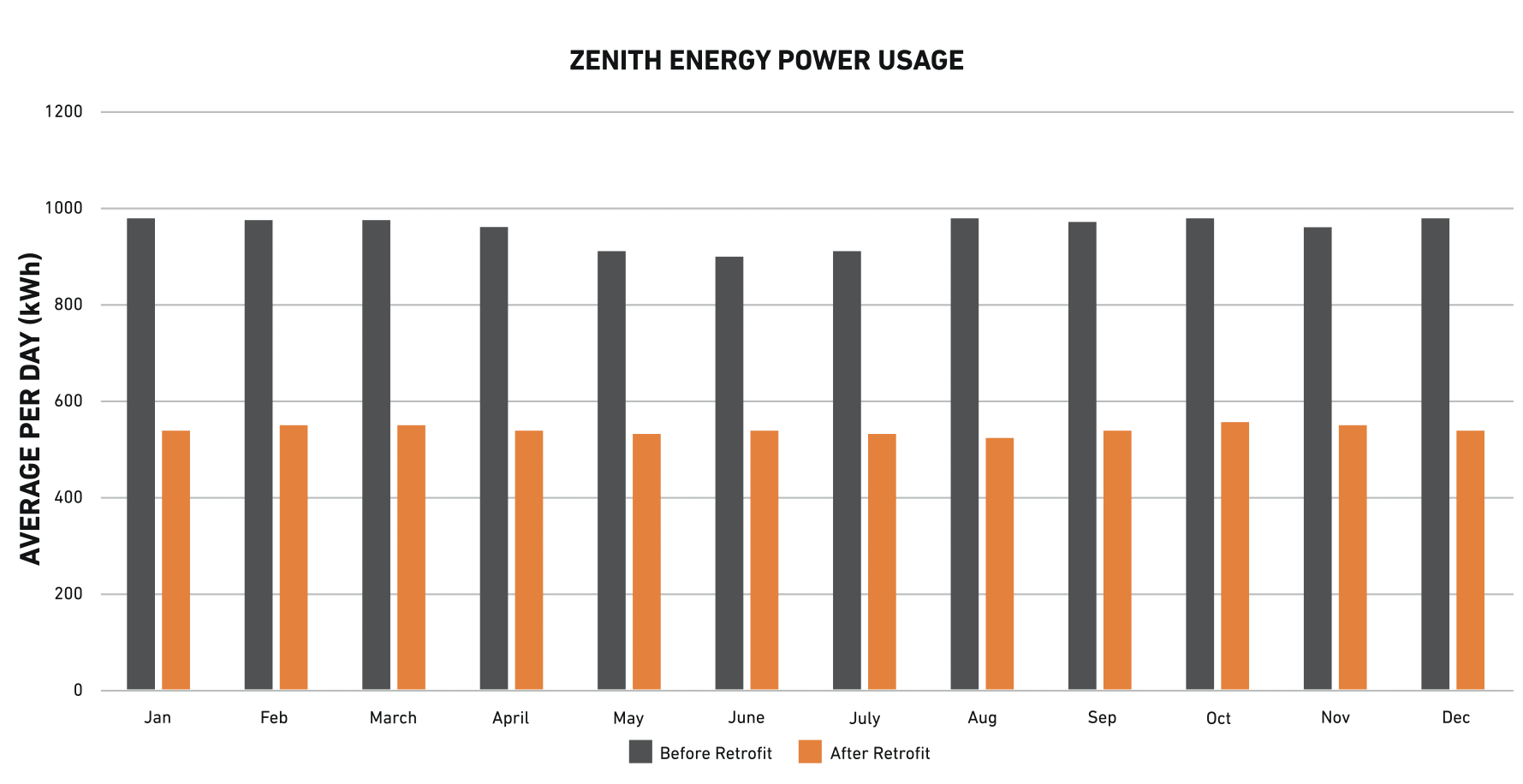
Upgrading A Terminal Vapor Recovery System
By Gayla Broostin, September 2022 Zenith Energy Power Usage Before and After Zeeco Retrofit..
Read More >>>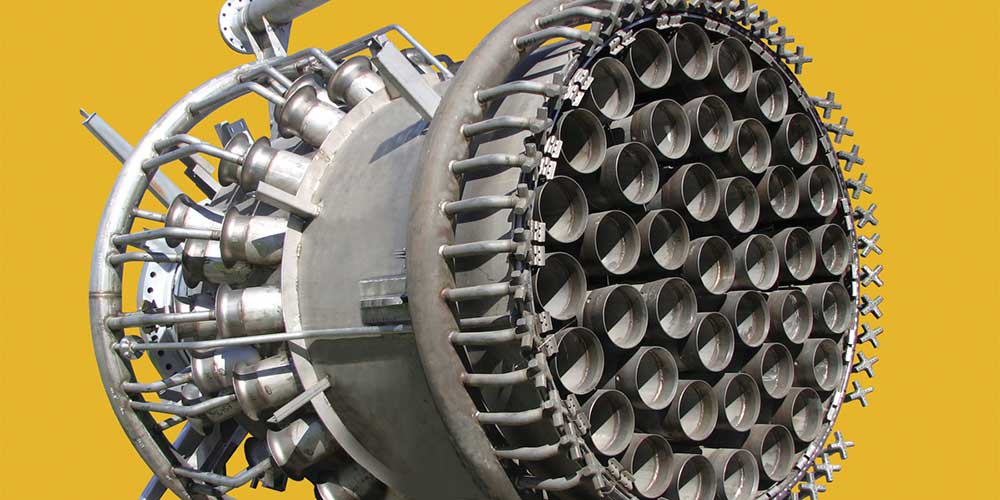
Flare Tip Upgrade Case Study
We want to thank Zeeco for an excellent job of building and delivering our new flare tip.
Read More >>>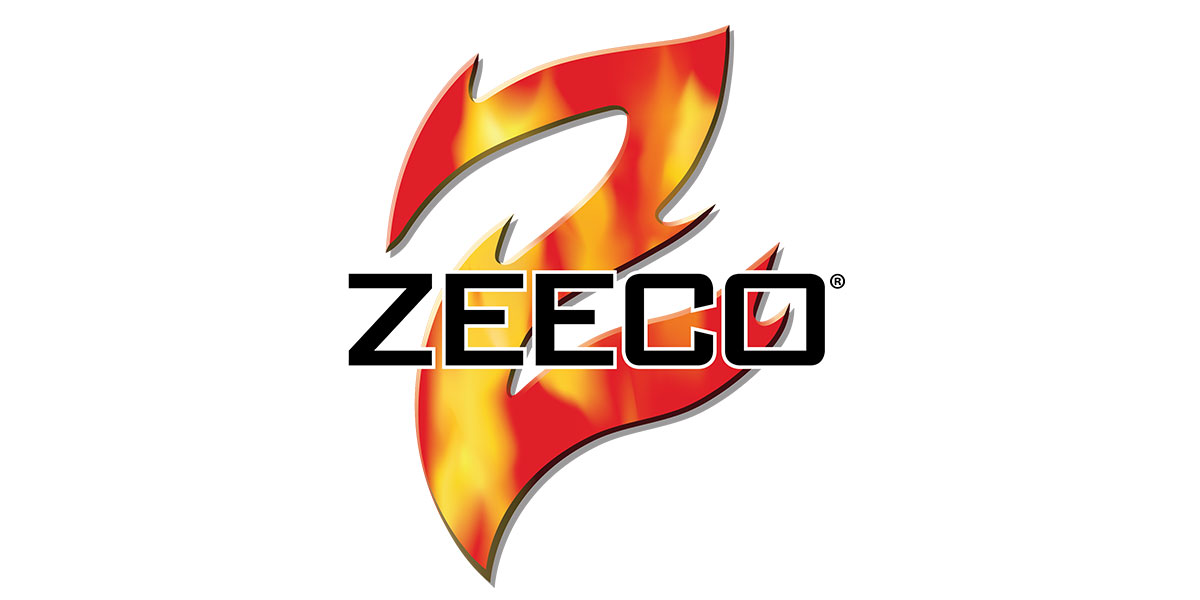
Tengizchevroil Case Study
Zeeco’s Aftermarket team was asked by Tengizchevroil to review the design of a steam flare tip used..
Read More >>>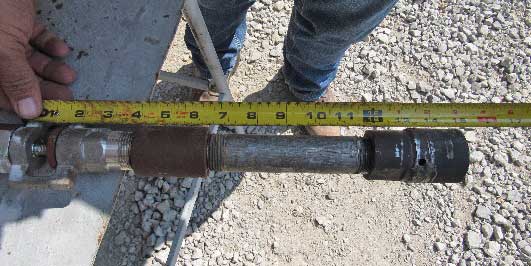
Dialed-In: Expedited Pilot Replacement
Heroic response leads to robust retrofit of Hengli PDH Air Heater
Read More >>>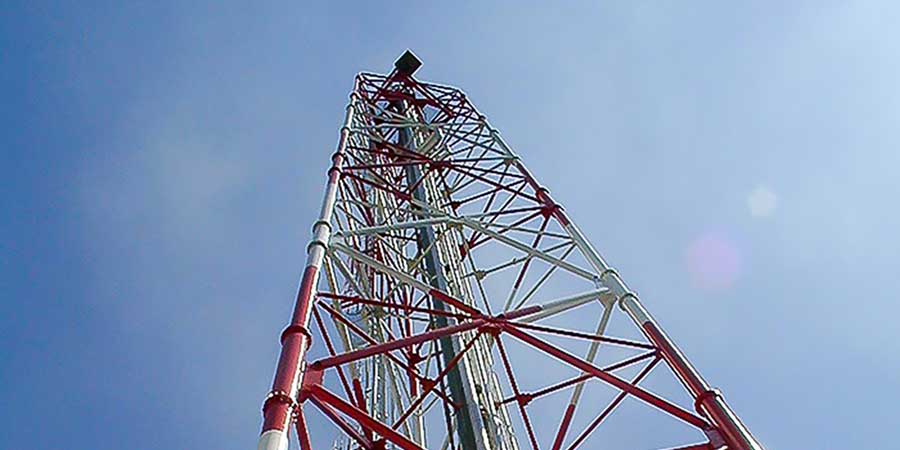
LG Chemical Korea Case Study
In 2012, Zeeco successfully installed a Zeeco QFSC Steam Assisted Flare System for LG Chemicals..
Read More >>>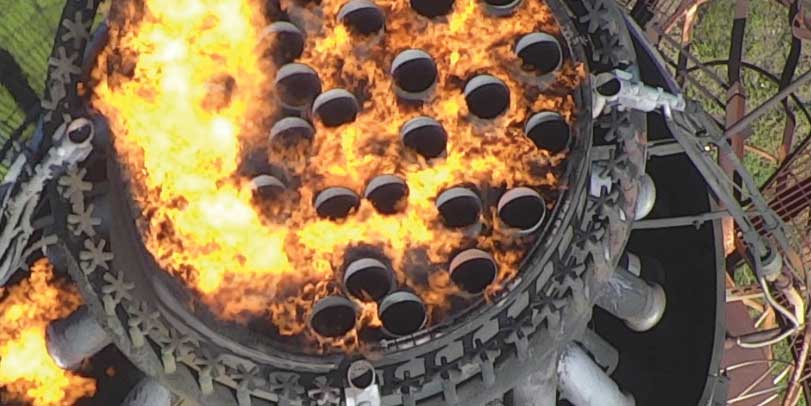
Record Breaking Delivery: Hurricane Harvey Relief
In August 2017, one of the costliest and most destructive hurricanes in American history, Hurricane..
Read More >>>